Liquid Filters
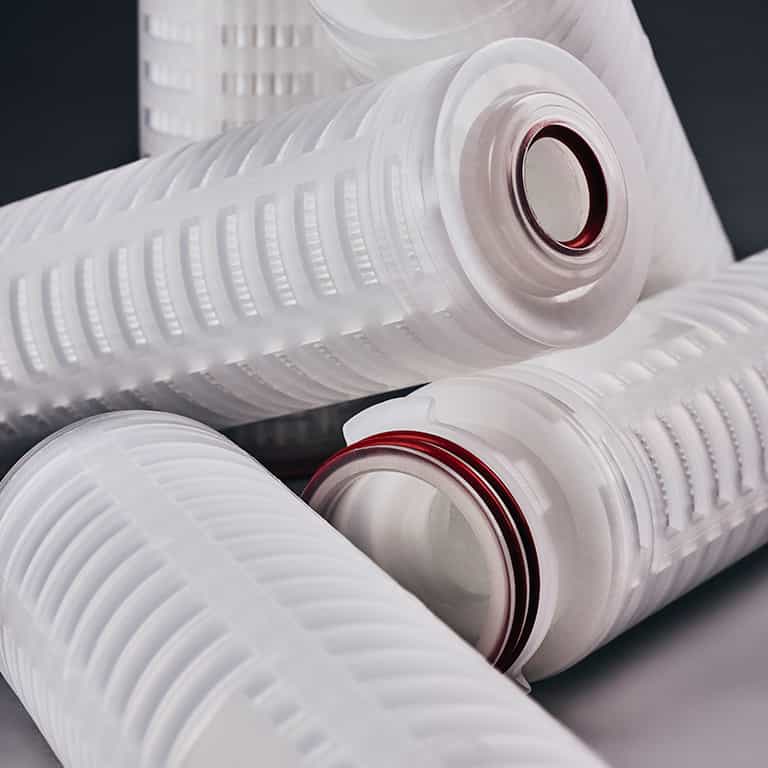
Graver Technologies specializes in designing, engineering, and manufacturing a comprehensive line of high-performance and cost-effective filter cartridges and housings for liquid process filtration. Serving a variety of industries—such as food and beverage, chemical, microelectronics, and healthcare—our solutions are tailored to meet diverse application needs.
Key liquid process filters include:
- Melt Blown Depth Filters: Designed for applications requiring reliable depth filtration.
- Resin Bonded Filters: Ideal for high-temperature applications and resistant to a wide range of chemicals.
- Microfiberglass and Polypropylene Pleated Cartridges: Provide an extensive filtration area for high efficiency and longer service life.
- Membrane Filters with PTFE or Polyethersulfone (PES): Perfect for critical applications requiring precise filtration and high purity.
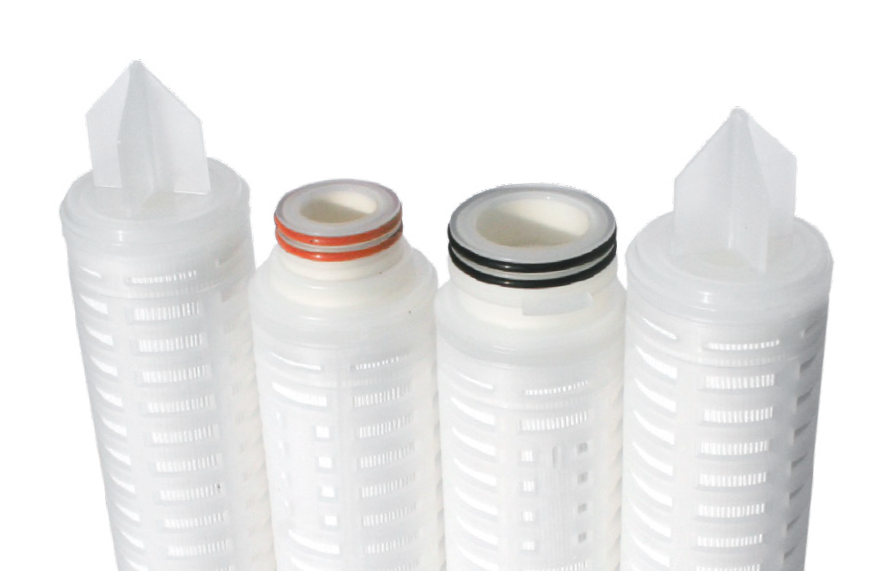
ZTEC™ SLWB Series
ZTEC SLWB Serial Layer cartridge filters utilize dual layer TECpore polyethersulfone membrane to provide consistent removal of spoilage organisms and inorganic particulate to protect your beverage from spoilage.
- Manufactured with Graver Technologies’ high performance TECpore PES membrane in an ISO Class 7 Cleanroom Environment
- 100% flushed with ultrapure DI water
- Serial layer PES membrane is two filters in one greatly extending life for greater throughput, improved efficiency, reduced clogging
- Repeatably Steamable/Sanitizable
- High log reduction values for spoilage organisms
- Quick wet treatment available
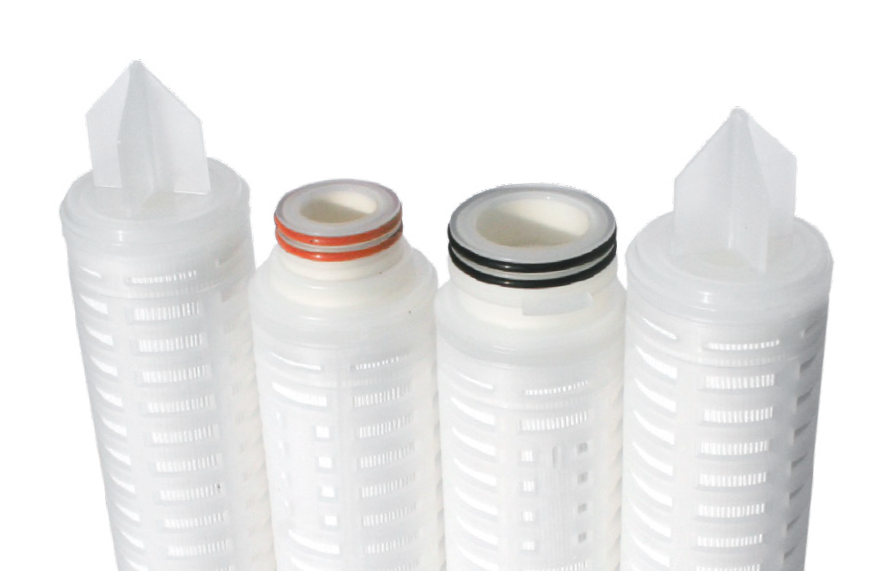
ZTEC™ SLB Series
ZTEC SLB Serial Layer Bioburden Reduction grade membrane cartridges is made with two matched layers of TECpore® to provide consistent and lasting performance for bioburden reduction and particle removal across a wide range of beverage, pharmaceutical and biological fluids.
- Manufactured with Graver Technologies’ high performance TECpore PES membrane in an ISO Class 7 Cleanroom Environment
- 100% flushed with ultrapure DI water
- Serial layer PES membrane is two filters in one greatly extending life for greater throughput, improved efficiency, reduced clogging
- Repeatably Steamable/Sanitizable
- High retentions up to 107/cm2 challenged for bacteria and yeast
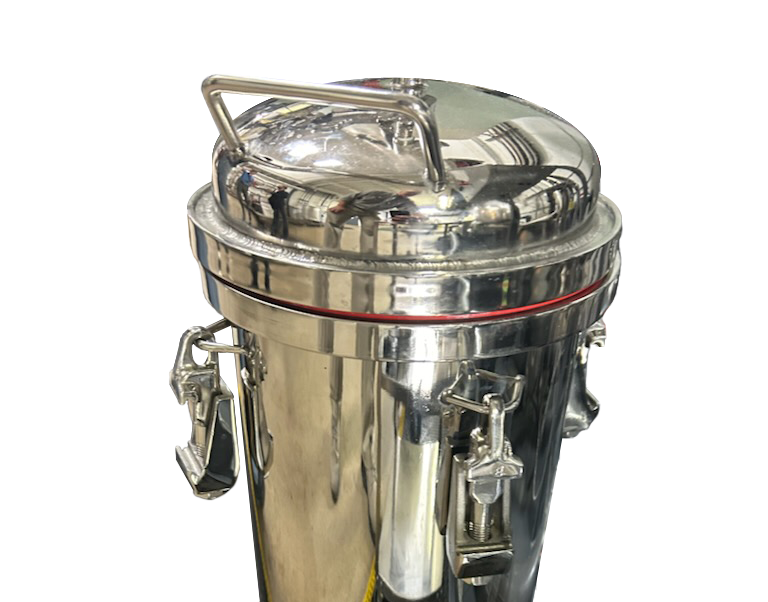
High Flow RF Series Filter Housing
Graver High Flow RF Series filter housings are designed to accept Graver's and competitive High Flow RF Series large geometry filter elements. Available in both vertical and horizontal orientations, the High Flow RF housings are available in designs to accommodate from 1 to 15 filter elements, from 10" to 60" long. Constructed of 304 or 319 stainless steel, standard design is rated for 150 PSIG (10.3 bar) with higher pressure design available upon request.
- Industrial grade housings available in 304L and 316L Stainless Steel wetted parts
- Designs for 1, 3, 4, 7, 10, 12, 15, filters per housing
- Single Round -Segment Screw hold down clamps; Multi-round -swing bolt hold down clamps
- 150 psig design
- Accepts 10", 20", 40" and 60" High Flow RF cartridges
- Vertical and horizonal designs available
- Vent and drain standard
- Hold Down plate prevents elements from unseating due to back pressure
.jpeg)
Stratum™ C Series
Stratum C Series filters are highly efficient and retain captured contaminants even at high differential pressures, delivering 99.9% efficiency at the stated micron.
- 90% Nominal retention ratings from 0.5 to 100 microns
- Multizone melt blown depth filter with a graded pore structure for maximum dirt holding capacity
- Thermally bonded fibers for high void volume and long onstream life
- Lot traceable filters come with certificate of conformance
- 100% pure virgin polypropylene
- Molded center core for higher temperature and pressure capability
- Free of surfactants, binders and adhesives
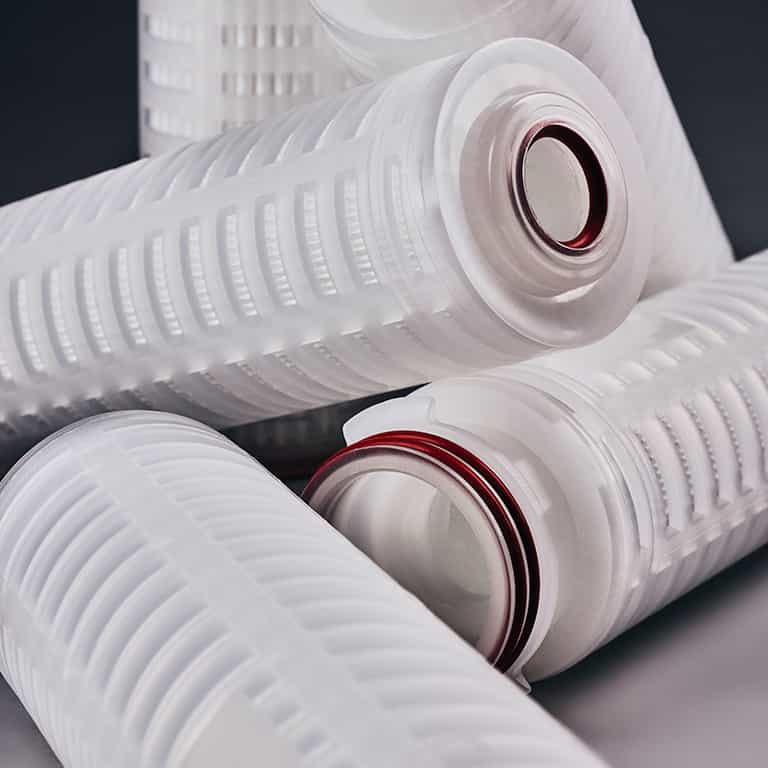
CelluTEC® HF Series
The CelluTEC is dual layered with cellulosic median that contains DE (Diatomaceous Earth) and polypropylene media to provide enhanced filtration
- Compact cartridge design to minimize space required
- 99% retention at rated pore size
- HF cartridge rated up to 30 GPM (114LPM) per 10" element for optimal filtration
- Thermally Bonded Construction
- High Solids Removal
- Excellent Product compatibility
.jpeg)
CelluTEC® Series
The CelluTEC is dual layered with cellulosic median that contains DE (Diatomaceous Earth) and polypropylene media to provide enhanced filtration
- Dual cartridge size available, standard 2.7" and High Flow RF 6"
- Compact cartridge design to minimize space required
- 99% retention at rated pore size
- HFRF cartridge rated up to 15GPM per 10" element for optimal filtration
- Thermally Bonded Construction
- High Solids Removal
- Excellent Product compatibility
.jpeg)
High Flow Housing-3/19
Graver High Flow Series filter housings are designed to accept Graver and competitive High Flow Series large geometry filter elements.
- Industrial grade housings available in 304, 316 and carbon steel wetted parts
- ASME U code available
- Designs for 1, 3, 4 or 7 filters per housing for flows up to 3500 GPM*
- 150 psig designs
- Accepts 20", 40" and 60" High Flow cartridges
- Vertical and horizontal designs offered
- Hold down plate prevents elements from unseating due to back pressure
- Filter removal tool available to facilitate element changeout
- Swing bolts on 150 psig design
- Equipped with 1" vent and 2" drain (1" drain on tipped horizontal style)
.jpeg)
PMC® Series
The pleated filter cartridge has utilizes polypropylene media with high surface area, allowing for greater system flow rate. It's affordable & made for a range of applications.
- Micron ratings from 0.2 to 50 μm — Broad application range
- Fixed pore structures — Resists unloading of captured contaminant
- Polypropylene Construction — Inert to many process fluids
- Various Gasket/ORing materials — Compatible with a variety of fluids
- Economically efficient filtration
- Manufactured in continuous lengths up to 40 inches
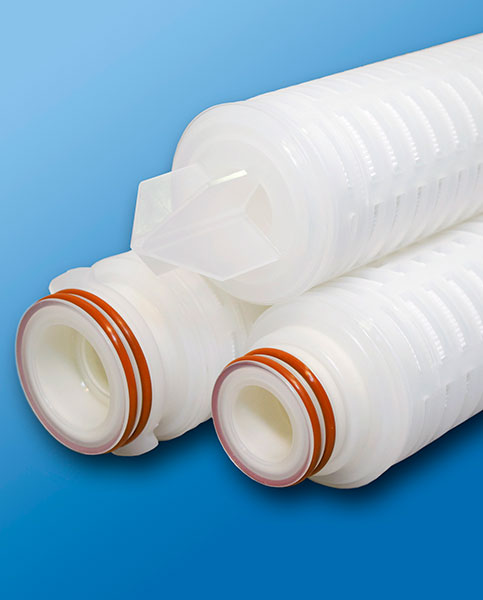
ZTEC™ P Series
ZTEC™ P Sterilizing Grade membrane cartridges are validated for complete bacterial retention to yield product sterility in biopharmaceutical final filtration applications.
- Manufactured in an ISO Class 7 Cleanroom Environment
- 100% flushed with ultrapure DI water
- Meets ASTM Standards for Sterility
- Repeatably Steamable/Sanitizable
- 100% Integrity tested prior to release
- Pore size, lot and serial number are stamped on each filter element for identification and traceability
- Complete validation guide available
.jpeg)
Stratum™ A Series
Stratum A Series filters are highly efficient and retain captured contaminants even at high differential pressures, delivering 99.9% efficiency at the stated micron.
- Absolute retention ratings from 0.3 to 100 microns
- Multizone melt blown depth filter with a graded pore structure for maximum dirt holding capacity
- Thermally bonded fibers for high void volume and long onstream life
- Lot traceable filters come with certificate of conformance
- 100% pure virgin polypropylene
- Molded center core for higher temperature and pressure capability
- Free of surfactants, binders and adhesives
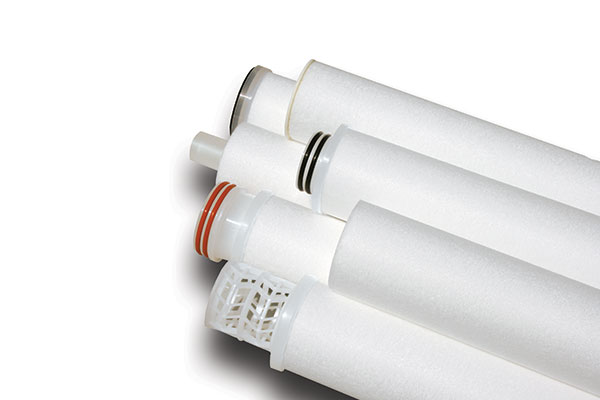
MBC™ Series
An economical, nominally rated disposable filter element constructed of 100% polypropylene media for chemical compatibility with a variety of process fluids.
- Available in nominal ratings from 1 to 75 microns
- Molded core for excellent collapse strength
- Graded pore construction for long onstream life
- Melt blown media resists dirt unloading as differential pressure increases
- Non-shedding
- High dirt holding capacity
- Economical depth filtration
- Thermal bonded endcaps optional
- Free of binders, adhesives and surfactants
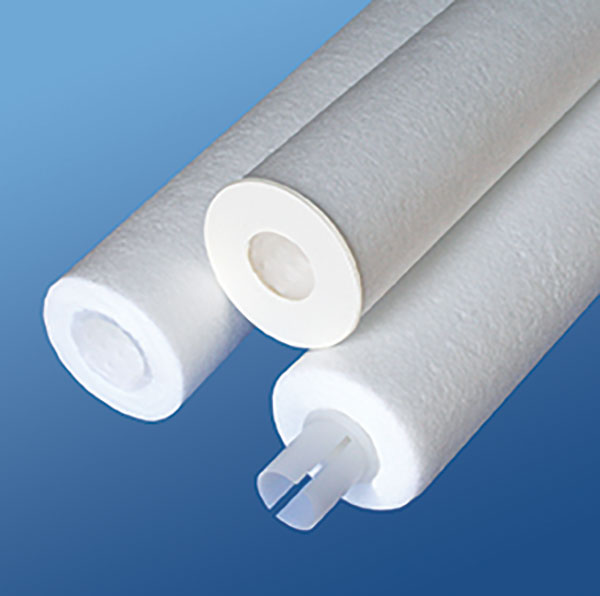
Crystal MBF Series
Use this document to explore Crystal MBF Series Filter Cartridges.
- Available in nominal ratings from 1 to 75 microns
- Formed Crystal Core for excellent collapse strength
- Graded pore construction for long on-stream life
- Melt blown media resists dirt unloading as differential pressure increases
- Non-shedding
- High dirt holding capacity
- Economical depth filtration
- Free of binders, adhesives and surfactants
- Highly consistent performance
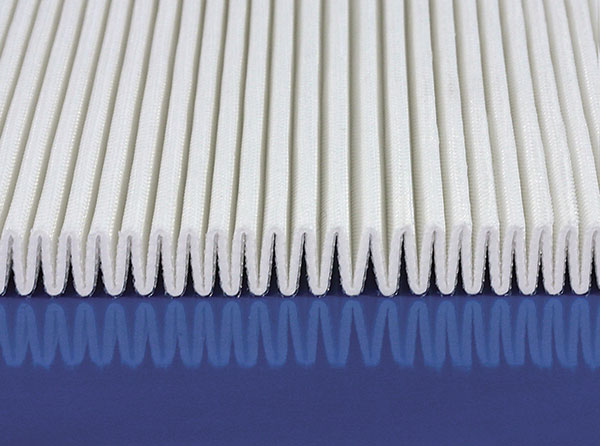
QXL™ Series
QXL™ depth filter has an extra-loft configuration for industrial solutions with agglomerated particles, gels, and high viscosity, offering absolute retention performance.
- Hybrid pleated depth construction combines graded pore structure with high surface area.
- Constructed entirely of polypropylene — Compatible with a broad range of solutions and chemicals
- Optimized pleat configuration — Provides the ideal combination of retention, flow rate and throughput
- Excellent gel and agglomerated particle retention reduces defects
- Available in common end cap configurations — Retrofits easily into most filter housings
.jpeg)
QMC™ Series
This innovative product has melt-blown polypropylene media with multiple layers, providing high flow rates and ideal depth filtration.
- Micron ratings from 0.1 to 10 μm — Broad application range
- High Filtration Efficiency — 95%
- Graded pore structure — Multilayer, media for high dirt holding capacity
- Fixed pore construction — Resists dirt unloading at maximum differential pressure
- Polypropylene construction — Inert to many process fluids
- Various Gasket/Oring materials — Compatible with many fluids
.jpeg)
QMA™ Series
This filter is constructed with a high surface area melt blown polypropylene media for low initial pressure drop, high dirt holding capacity, and efficiency performance.
- Micron ratings from 0.2 to 20 μm — broad application range
- “Absolute” Efficiency — rated at 99.98% (Beta 5000)
- High surface area — high flow rate, and long service life — minimize maintenance cost
- Fixed pore construction — resists dirt unloading at maximum differential pressure
- Polypropylene construction — inert to many process fluids
- Various gasket/Oring materials — compatible with many fluids
- Heavy duty molded cage — high structural strength
- Highly consistent melt blown media for consistent performance
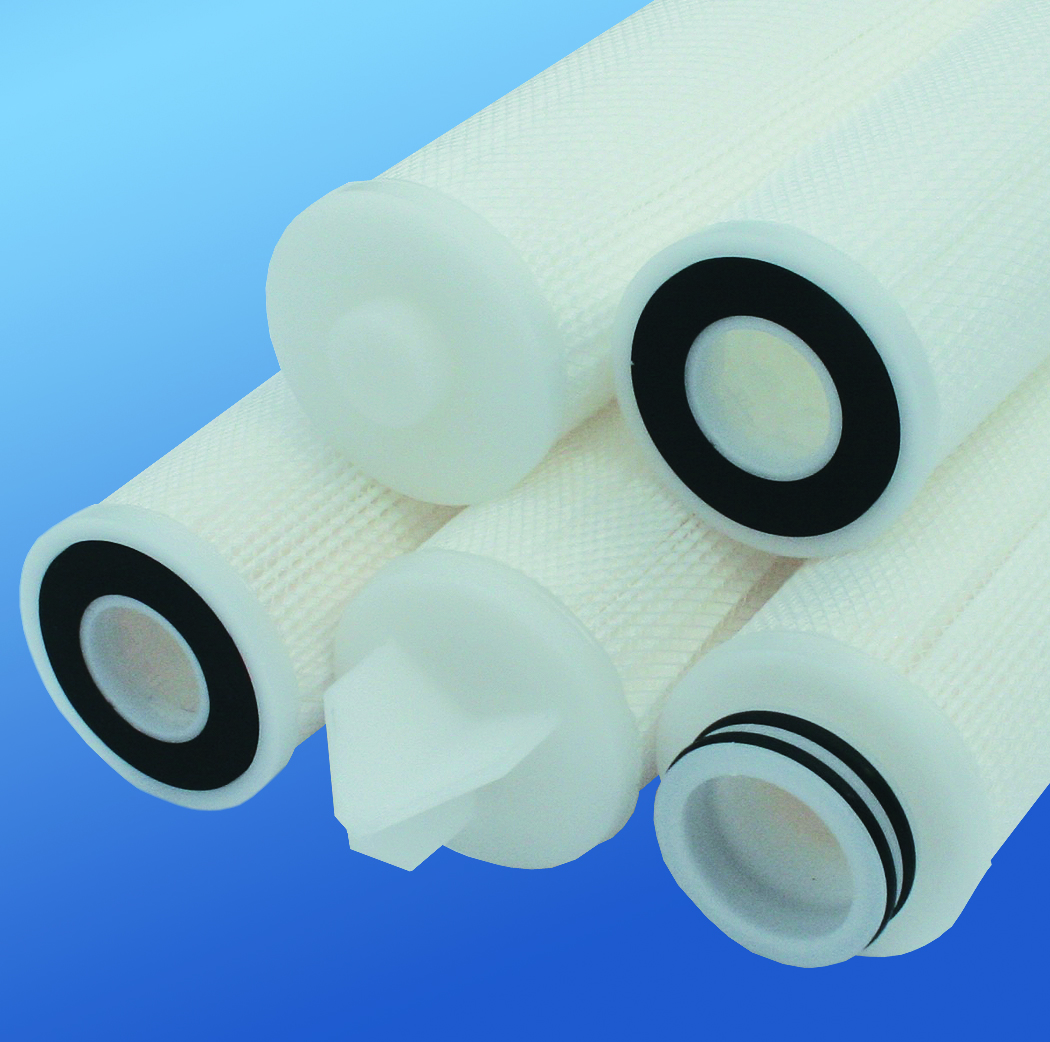
PMG™ Series
This high efficiency, economical filter element is constructed of pleated Borosilicate Microfiberglass media that combines excellent flow rates with exceptional service life to support a wide range of chemical and industrial applications
- Micron ratings from 0.2 to 30 μm — Broad application range
- Uniform pore structures — High removal efficiency
- Various Gasket/ORing materials — Compatible with a variety of fluids
- Economically efficient filtration
- Manufactured in continuous lengths up to 40 inches
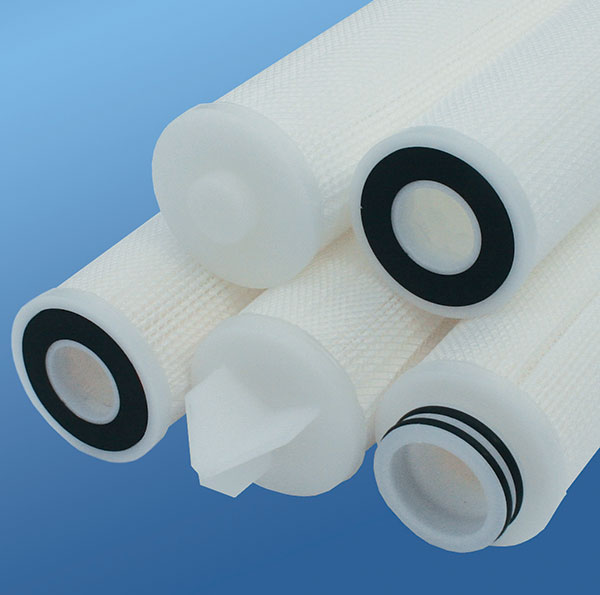
PME™ Series
For applications requiring an economical solution, choose the PME Series to deliver absolute efficiency in a broad range of particle sizes. This all polypropylene filter is suitable for a wide range of applications and provides industry certifications to satisfy most critical requirements.
- Micron ratings from 0.2 to 50 μm — Broad application range
- 2.55" diameter to fit installed housings with ease
- “Absolute” Efficiency — Rated at 99.98% (Beta 5000)
- Optimized surface area — High dirt holding for long service life
- Fixed pore structure — Eliminates dirt unloading at maximum differential pressure
- Polypropylene Construction — Inert to many process fluids
- Various Gasket/O-Ring materials — Compatible with a variety of fluids
- Manufactured in continuous lengths up to 40 inches
.jpeg)
PMA™ Series
The all polypropylene filter retains particles with absolute efficiency and is available in various pore sizes, suitable for a wide range of applications.
- Micron ratings from 0.2 to 100 μm — Broad application range
- “Absolute” efficiency — Rated at 99.98% (Beta 5000)
- Competitive surface area — High flow rates, and long online service — minimize maintenance cost
- Fixed pore structure — Eliminates dirt unloading at maximum differential pressure
- Polypropylene construction — Inert to many process fluids
- Various gasket/Oring materials — Compatible with a variety of fluids
- Manufactured in continuous lengths up to 40 inches
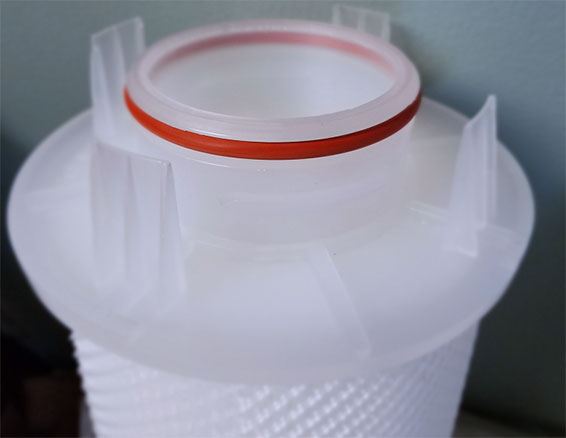
High Flow RF
Graver High Flow RF Series filter is another in the series of larger geometry filters to handle higher volume applications with fewer filter elements.
- 6.5" diameter, large geometry for high flow rates
- Absolute retention ratings from 1 to 100 microns
- Capable of flow rates up to 80 GPM in the P2 configuration and 500 GPM in the P30 configuration
- Multilayer pleated construction with optimized surface area
- Retrofits competitive large diameter filter housings utilizing the “740” design or the large diameter 338 oring design
- Thermally bonded construction
- All polypropylene construction provides for a high level of chemical compatability
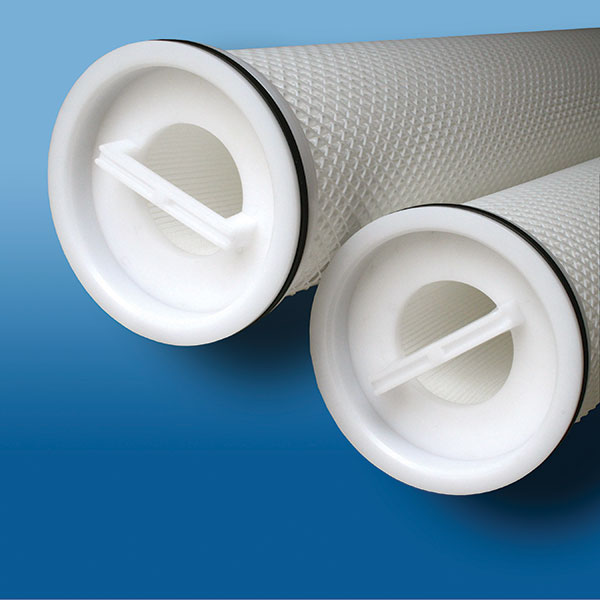
High Flow GF
Graver High Flow GF Series filters features microfiber glass media in a larger geometry to handle higher flows with fewer filter elements.
- Materials of construction allow compatibility with some chemistries not served by all polypropylene elements
- 6" diameter, large geometry for high flows
- Absolute retention ratings from 1 to 20 microns
- Capable of flow rates up to 500 GPM in a single 60" element
- Insideout flow retains contaminant even during changeout
- Outer cage prevents media extrusion problem experienced with some competitive offerings
- Unique Quad Seal gasket provides maximum seal integrity
- Retrofits competitive high flow filter housings
- Thermally bonded construction
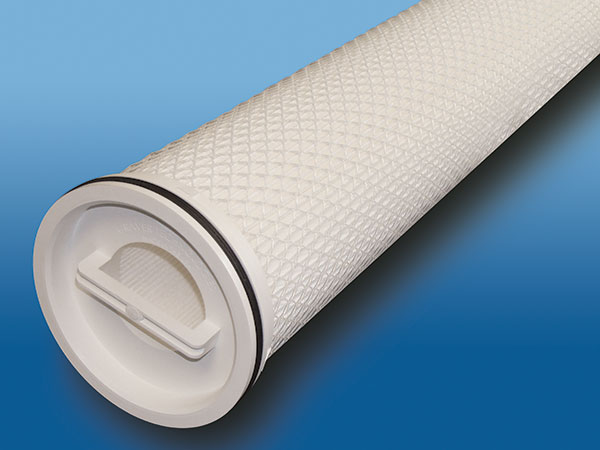
High Flow
Graver High Flow Series filters feature a larger geometry to handle higher flows with fewer filter elements. The result is much faster, easier filter changeouts.
- 6" diameter, large geometry for high flow rates
- Absolute retention ratings from 1 to 100 microns
- Capable of flow rates up to 500 GPM in a single 60" element
- Inside-out flow retains contaminant even during changeout
- Multi layer pleated construction with optimized surface area
- Outer cage prevents media extrusion problem experienced with somecompetitive offerings
- Unique Quad Seal gasket provides maximum seal integrity
- Retrofits competitive high flow filter housings
- Thermally bonded construction
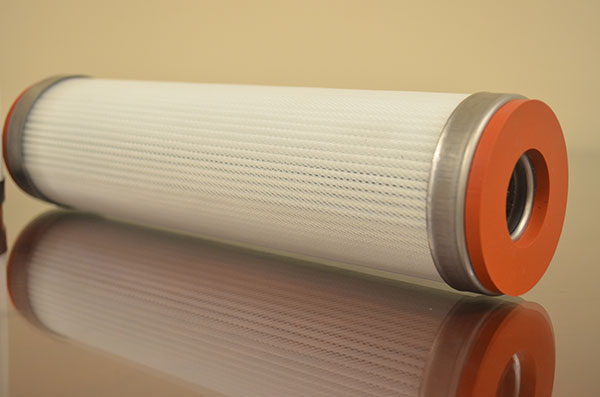
GSS™ Series Filter Cartridges
A Borosilicate Microfiber glass filter with stainless steel supports for high temperature applications
- 304 stainless steel center core and end caps — allows for high temperature applications
- Micron ratings from 0.2 to 30 μm — Broad application range
- Uniform pore size — High removal efficiency
- High surface area — High flow capability and dirt holding capacity
- Long service life — Minimizes maintenance costs
- Small diameter fibers — High flow rates at low pressure drops
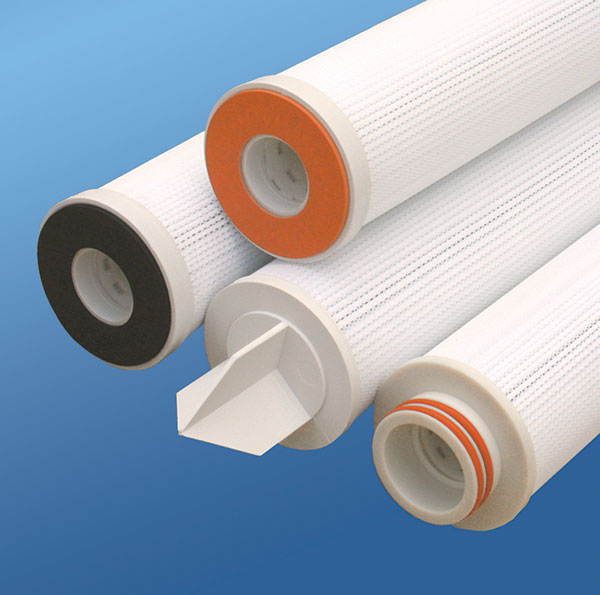
GFP™ Series
The cost-effective GFP™ filter element is constructed of pleated Borosilicate Microfiberglass media that combines excellent flow rates with exceptional service life.
- Polyester hardware extends application range beyond the limits of polypropylene.
- Higher temperature capability of 230°F (110°C)
- Micron ratings from 0.2 to 30 μm — Broad application range
- Uniform pore size — High removal efficiency
- High surface area — High flow capability and dirt holding capacity
- Long service life — Minimizes maintenance costs
- Fixed pore construction — Eliminates dirt unloading at maximum differential pressure
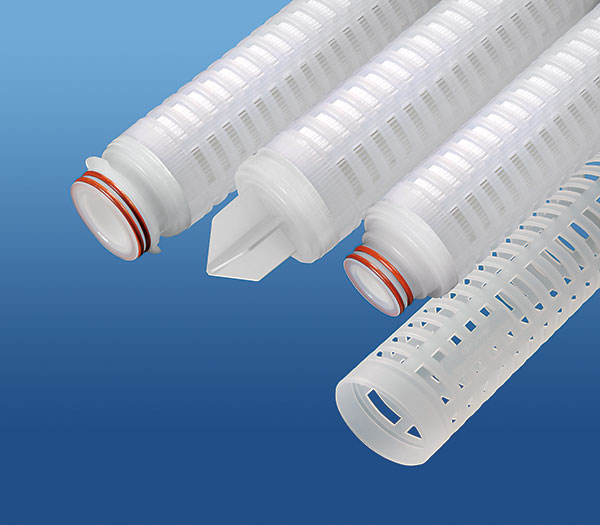
GFC™ Series
The cost-effective GFC™ filter element is constructed of pleated Borosilicate Microfiberglass media that combines excellent flow rates with exceptional service life.
- Micron ratings from 0.2 to 30 μm — Broad application range
- Uniform pore size — High removal efficiency
- High surface area — High Dirt Capacity
- Long service life — Minimizes maintenance costs
- Fixed pore construction — Eliminates dirt unloading at maximum differential pressure
- Small diameter fibers — High flow rates at low pressure drops
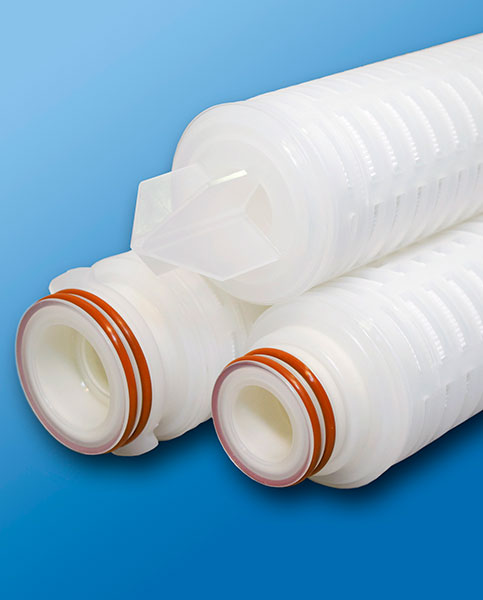
ZTEC™ WB Series
ZTEC™ WB cartridge filters use PES membrane to remove spoilage organisms and inorganic particulate to protect beverages.
- Manufactured in an ISO Class 7 Cleanroom Environment
- 100% flushed with ultrapure DI water and integrity tested
- Low adsorption of protein, color and flavor components
- Steamable/sanitizable for cleaning and reuse
- High log reduction values for spoilage organisms
- PES membrane provides high capacity contaminant loading
- Complete qualification guide available
- Quick wet treatment available
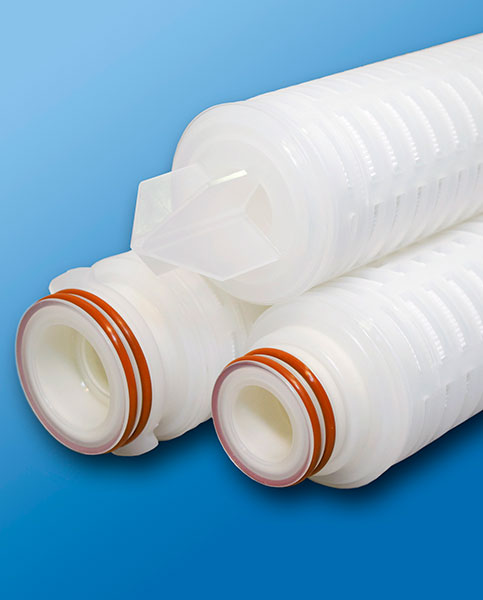
ZTEC™ G Series
This pleated, disposable filter element is constructed of absolute rated, hydrophilic, asymmetric polyethersulfone membrane with extended filter area.
- 7.0 ft2 (0.65 m2) of membrane surface area per 10" element — High throughput, longer online service reduces costly maintenance time
- Absolute rated membrane from 0.1 to 0.65 μm
- Manufactured in an ISO Class 7 cleanroom environment
- 100% flushed with 18 MΩ cm DI water and gross integrity tested
- Fixed pore construction eliminates dirt unloading as differential pressure increases
- Low extractables
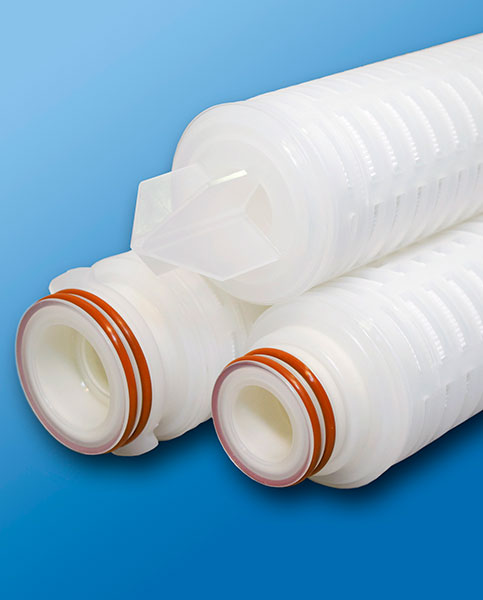
ZTEC™ E Series
The ZTEC™ E microelectronics grade cartridges by Graver are designed for ultrapure water filtration, and are hydrophilic and free of added surfactants to avoid contamination of water streams.
- Manufactured, flushed, tested and packaged, in an ISO Class 7 Cleanroom Environment
- Filters are 100% flushed with 18 MΩcm DI water and integrity tested
- Resistivity rinse up to 18 MΩcm and single digit ppb TOC levels with minimal throughput
- Available in a variety of end cap/adapter configurations to fit all industry standard housings
- Pore size, lot and serial number are stamped on each filter element for identification and traceability
- Complete qualification guide available
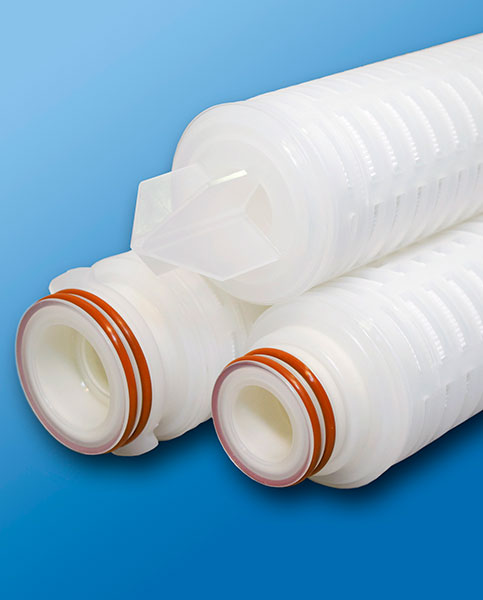
ZTEC™ B Series
ZTEC™ B Bioburden Reduction grade membrane cartridges provide highly consistent performance for bioburden reduction and particle removal across a wide range of beverage, pharmaceutical and biological fluids.
- Manufactured in an ISO Class 7 Cleanroom Environment
- 100% flushed with ultrapure DI water and integrity tested
- Repeatably steamable/sanitizable
- High retentions up to 107/cm2 challenged for bacteria and yeast
- Pore size, lot and serial number are stamped on each filter element for identification and traceability
- Complete qualification guide available
.jpeg)
WaterTEC™ Series
The WaterTEC™ filter series is constructed of absolute rated, hydrophilic, asymmetric polyethersulfone membrane and polypropylene components.
- Low pressure drop reduces energy costs
- High dirt holding capacity minimizes changeouts and down time
- All thermal bonded construction with no adhesives
- Available in all common configurations to allow use of existing filter housings
- Cost effective absolute filtration
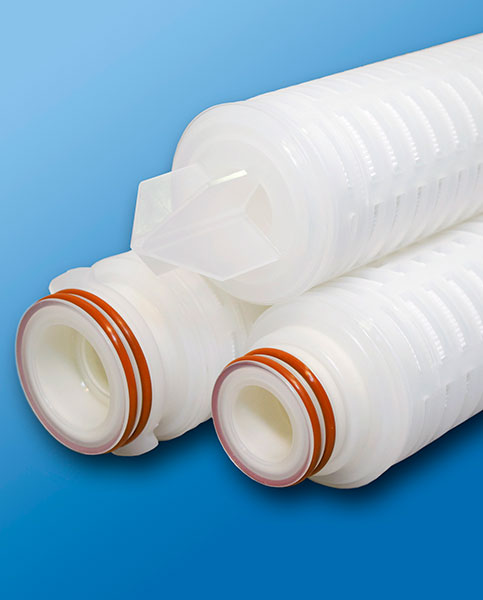
TefTEC™ V Series
TefTEC™ V cartridge filters are cost-effective with PTFE membrane & polypropylene support, ideal for compressed air and tank vent apps.
- Singlelayer construction provides superior flow rates and minimizes filtration system size
- 100% Flushed with 18 megohm DI water and integrity tested
- Filters are manufactured, flushed, tested and packaged in an ISO Class 7 Cleanroom Environment
- Each filter element stamped with pore size, lot and serial number for identification and traceability
- Demonstrated bacterial removal in air with an aerosol challenge level of 107
- Brevundimonas diminuta/10" cartridge
- Complete qualification guide available
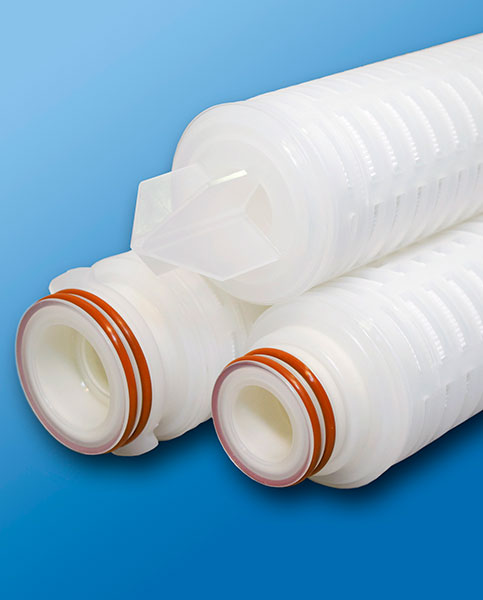
TefTEC™ Series
TefTEC™ filters have PTFE membrane & polypropylene components, offering superior hydrophobicity and cost-effective alternative to all-fluorocarbon filters.
- High surface area, singlelayer construction provides superior flow rates and minimizes filtration system size
- 100% Flushed with 18 MΩcm DI water and integrity tested
- Filters are manufactured, flushed, tested and packaged in an ISO Class 7 Cleanroom Environment
- Each filter element stamped with pore size, lot and serial number for identification and traceability
- Complete qualification guide available
- Available prewet for use with aqueous based chemicals
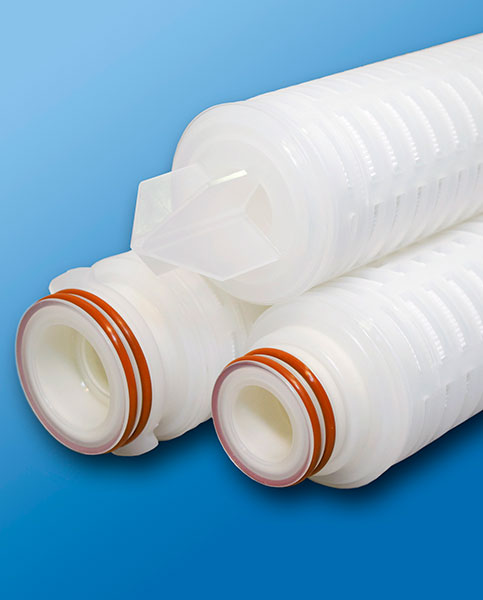
TefTEC™ P Series
TefTEC™ P membrane cartridges offer complete bacterial retention and product sterility for biopharmaceutical final filtration.
- Singlelayer construction provides superior flow rates and minimizes filtration system size
- 100% Flushed with 18 megohm DI water and integrity tested
- Filters are manufactured, flushed, tested and packaged in an ISO Class 7 Cleanroom Environment
- Each filter element stamped with pore size, lot and serial number for identification and traceability
- Complete bacterial removal in liquid at a challenge level of 107 /cm2 Brevundimonas diminuta
- Retentive for aerosolized virus
- Validation guide available
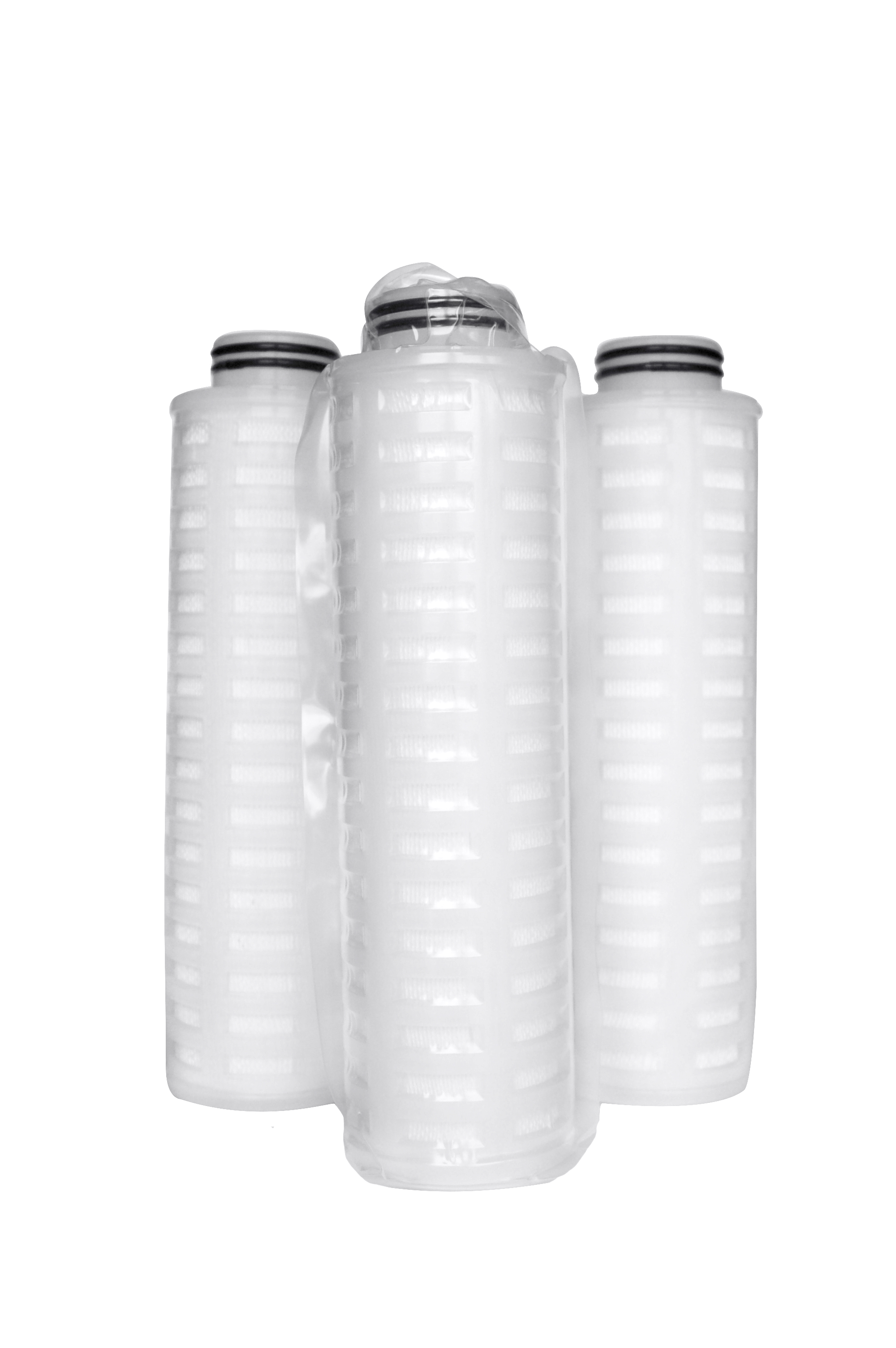
Citadel® Series
Citadel pleated membrane cartridges feature a PTFE membrane and PFA structural components to provide excellent chemical and temperature resistance for aggressive chemical applications such as etchers, strippers, cleaners and bulk chemicals.
- Manufactured, flushed, tested and packagedin an ISO Class 7 Cleanroom Environment
- Filters are flushed with 18 MΩ-cm DI water toensure low extractables and low particle shedding
- 100% integrity tested to provide reliable performance
- Resistivity rinse-up to 18 MΩ-cm and single digitppb TOC levels with minimal throughput
- Pore size ratings from 0.05 to 10 micronto meet a broad range of applications
- Wet-Pack option available to eliminate the requirementfor solvent pre-wetting in aqueous applications
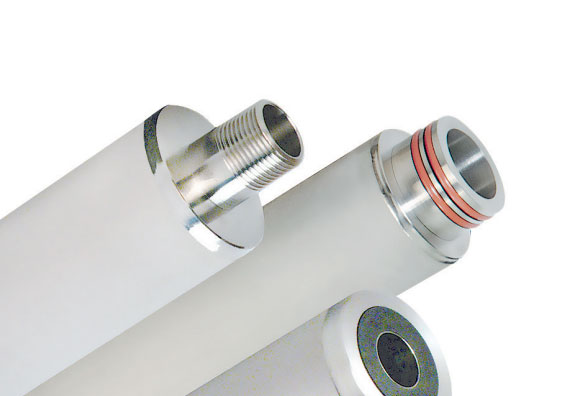
TPE™ Series
TPE™ filters are rugged metal filters that withstand temperature extremes, high pressures, and corrosive substances, suitable for various liquid and gas applications.
- Constructed entirely of sintered titanium or 316 Stainless
- Steel powder — offers high corrosion resistance
- Cleanable/backwashable — allows for reuse, maximum economy
- High temperature sintering — no media migration, high pressure capabilities
- Various gasket/ORing materials and configurations — easily retrofits most systems
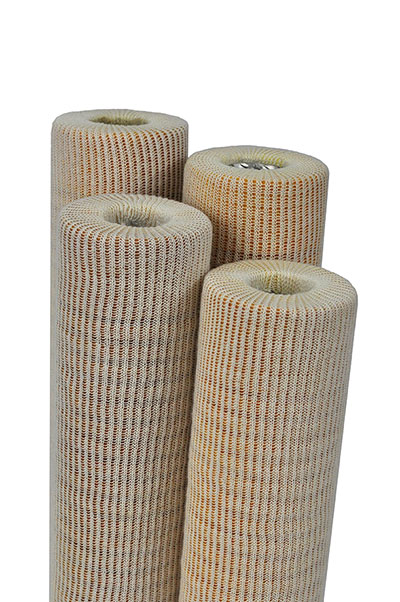
RTEC™ G Series
The RTEC™ G Series filters have microfiberglass/phenolic resin construction for a rigid pore structure that withstands temperature/viscosity extremes.
- Rigid microfiberglass/phenolic resin construction prevents unloading even at high differential pressures
- Grooved outer surface increases surface area for longer on-stream life
- Available in a wide range of removal efficiencies from 0.5 to 150 microns
- Broad chemical compatibility
- Provided with outer cotton wrap to aid in handling and protect the surface
.png)
GLP™ Series
The GLP Series filter housings are constructed of durable stainless steel and meet general purpose industrial and commercial filtration needs.
- Durable 316 stainless steel for corrosion resistance
- Vband clamp or swing bolts for quick and easy cartridge changeouts
- Accepts 10", 20", 30" and 40" cartridges with DOE, 222 and 226 configuration options
- Accommodates up to 2 3/4" OD cartridges
- Universal design has components to allow both DOE and 222 oring cartridge configurations to be used
.jpeg)
High Flow Series
The High Flow Series filters handle high flows with fewer elements and offer excellent dirt holding capacity. Smaller systems are possible, reducing upfront costs.
- 6" diameter, large geometry for high flow rates
- Absolute retention ratings from 1 to 100 microns
- Capable of flow rates up to 500 GPM in a single 60" element
- Insideout flow retains contaminant even during changeout
- Multi layer pleated construction with optimized surface area
- Outer cage prevents media extrusion problem experienced with some competitive offerings
- Unique Quad Seal gasket provides maximum seal integrity
- Retrofits competitive high flow filter housings
- Thermally bonded construction
.png)
GSC™ Series
The GSC Series of single cartridge metal filter cartridge housings are constructed of 316 stainless steel with a clamp closure to service a wide range of general purpose filter applications.
- Single shell construction for quick spillfree cartridge replacement
- Inline ¾" and 1" inlet/outlet connections for ease of installation
- Drains/Vent built in
- Flow rates of up to 7 GPM (26.5 lpm) per 10" filter cartridge
- Housing pressure drop is 0.6 PSID at 7 GPM (40mbar @ 26.5 lpm)
- Mounting bracket available
.png)
GHP™ Series
The GHP Series filter housings are made of 316L stainless steel and engineered using 3A standards for filtration applications requiring high purity production streams.
- Durable 316L stainless steel for corrosion resistance
- Vband clamp or swing bolt for quick and easy cartridge changeouts
- Accepts 5", 10", 20", 30"and 40" cartridges with DOE, 222/226 configuration options
- Accommodates up to 2 3/4" OD cartridges
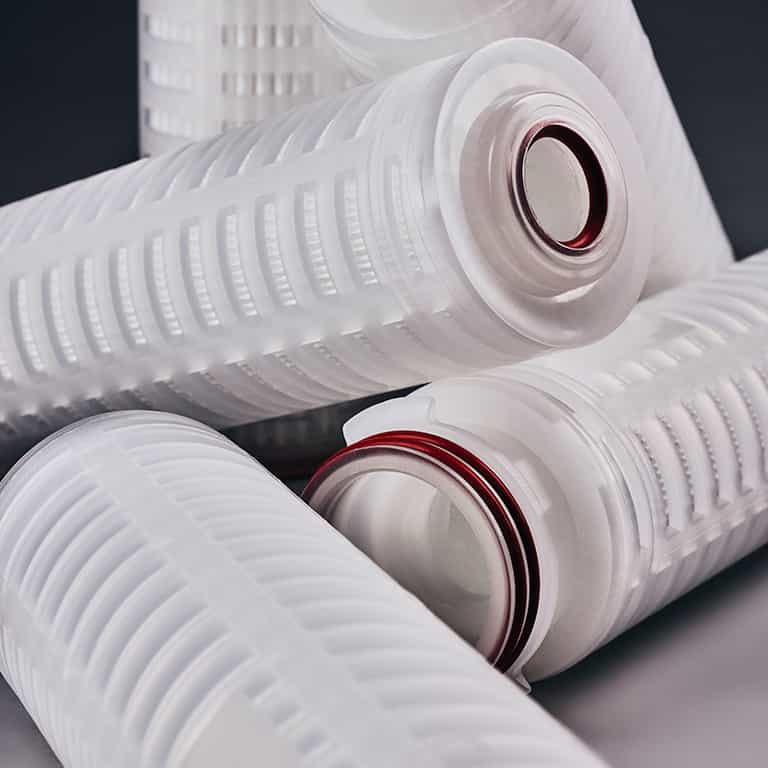
LPF Line Card
This document explores Graver Technologies' liquid process filters product offering.
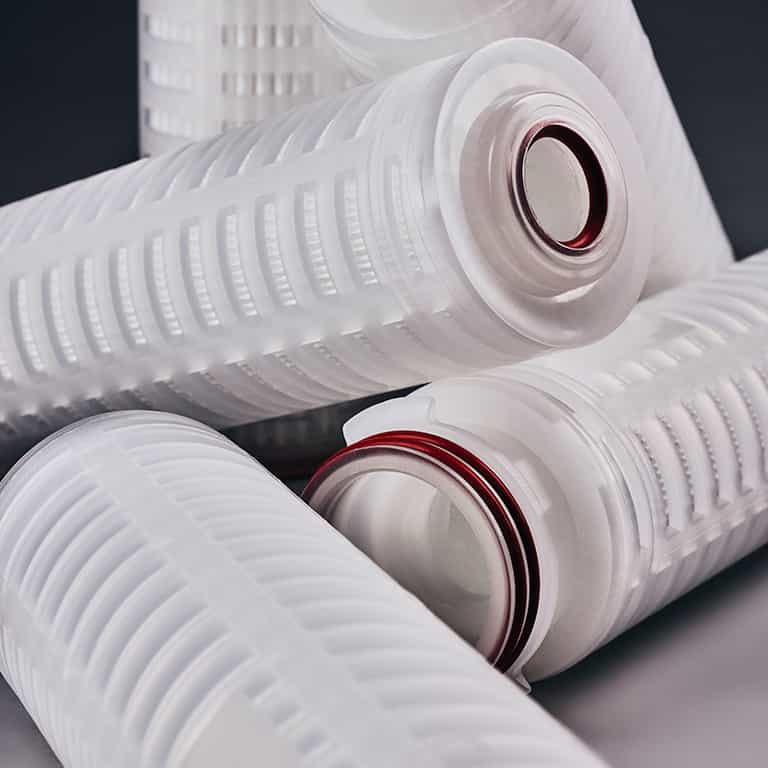
Beverage Brochure
Explore Graver Technologies wide range of filtration solutions, including specialized filters for the beverage industry, ensuring high-quality filtration for producers of water, wine, beer, soft drinks, as well as municipal water systems.
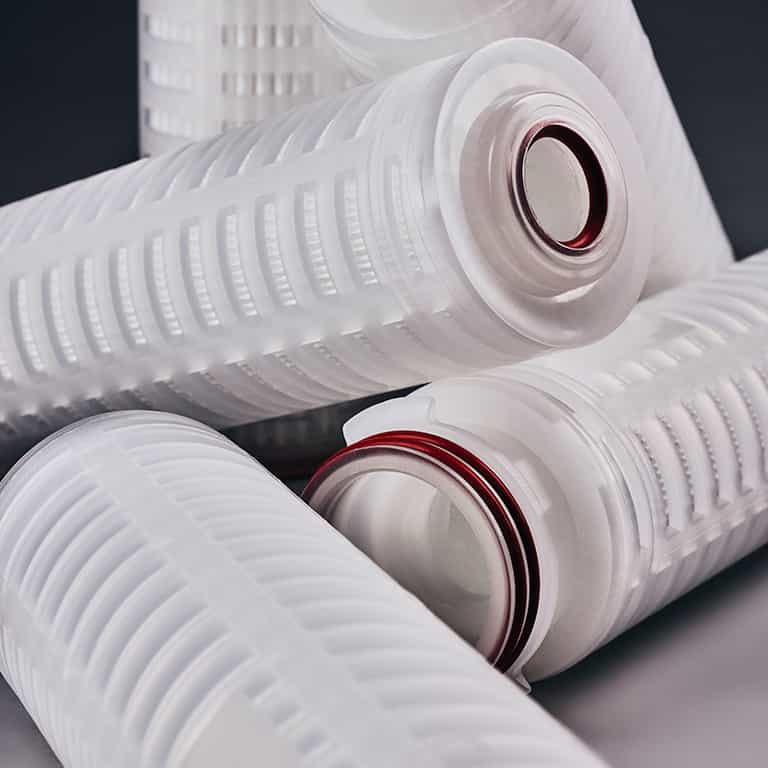
Healthcare Brochure
This pharma brochure explores critical filtration for the healthcare industry.
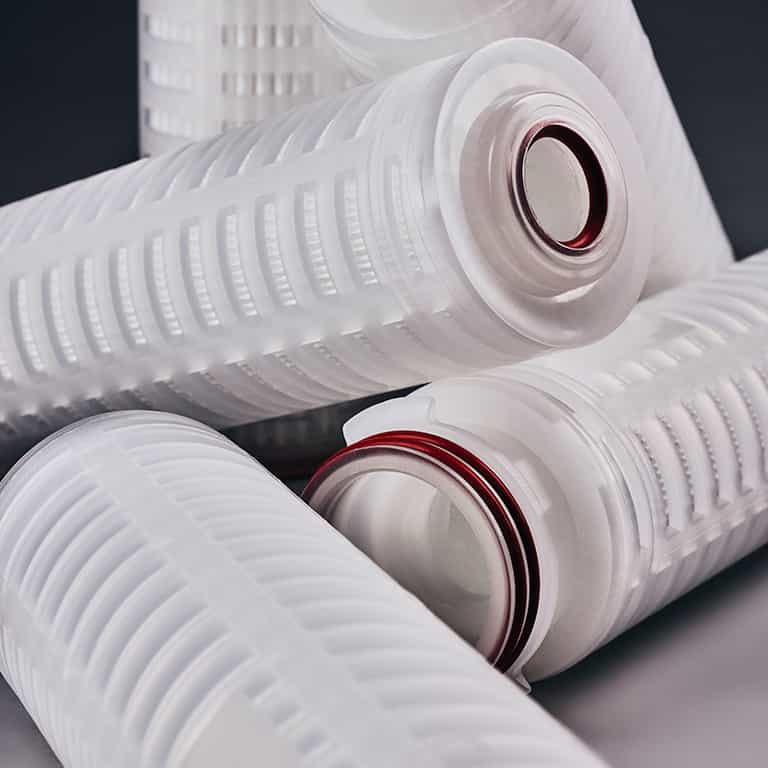
TB-009 USP, FDA, NSF
Use this technical brief to better understand USP, FDA, and NSF.
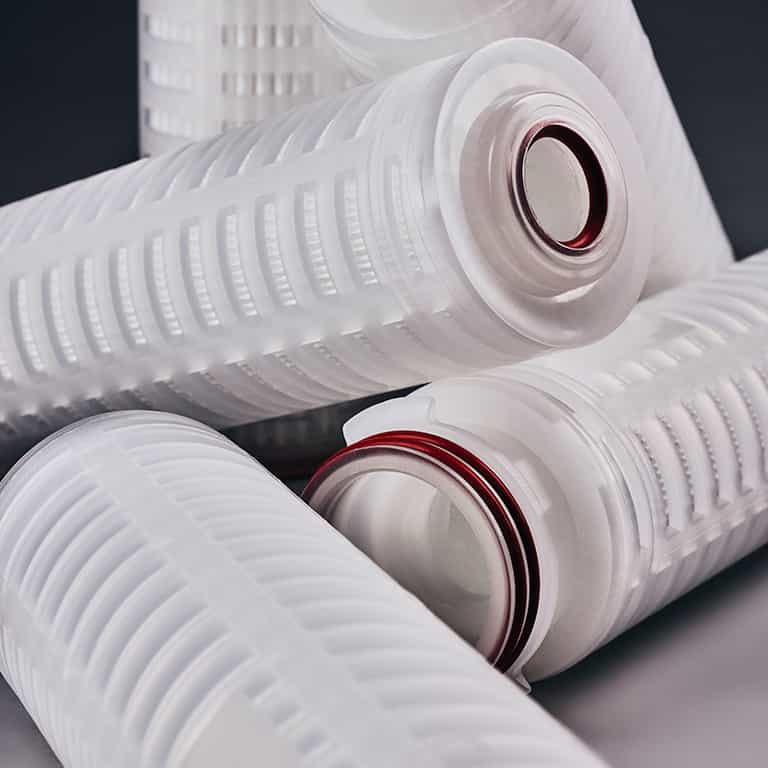
TB-020 Flavors and Extracts
This document discusses the production of flavors, focusing on natural flavors derived from various sources and the importance of filtration in ensuring high-quality flavor compounds for use in consumer products.
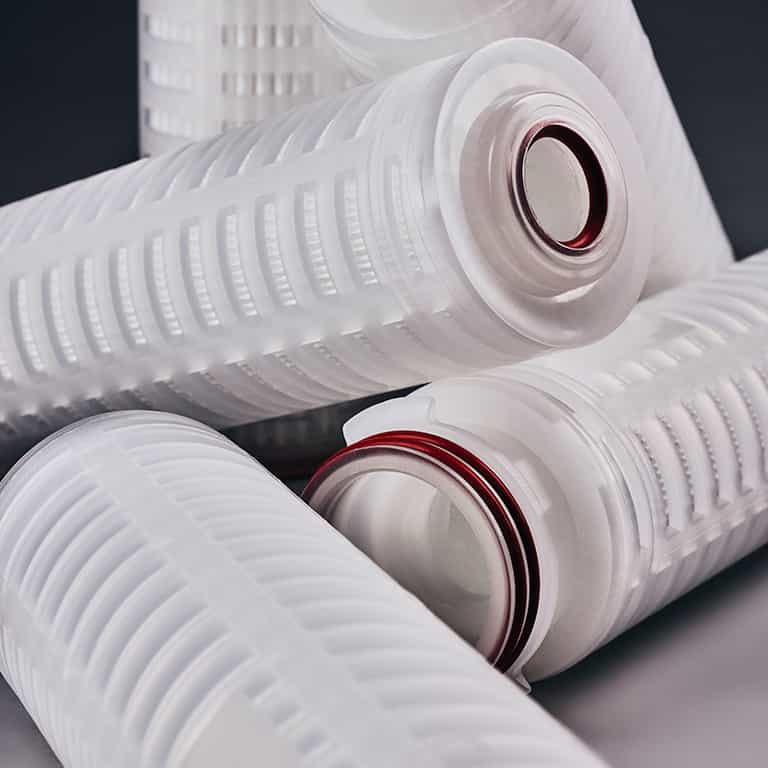
TB-021 Filtration Housings
This document provides an overview of filtration vessels and their importance in various industries, including healthcare, microelectronics, and refineries.
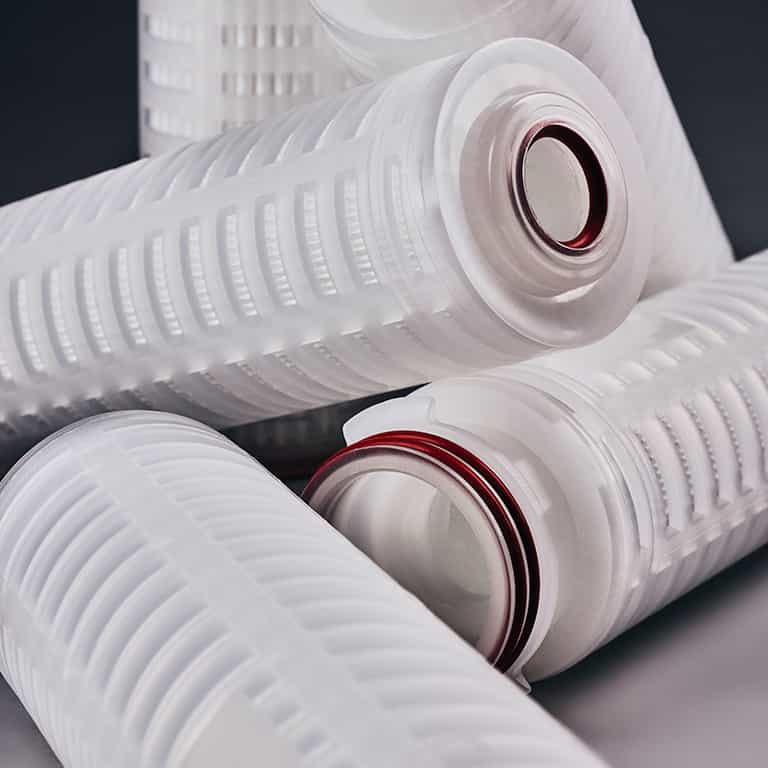
TB-024 System Sizing
This document discusses the concept of diminishing returns in filtration processes across various industries and provides insights into optimizing filter change-out strategies based on differential pressure and available filter area.
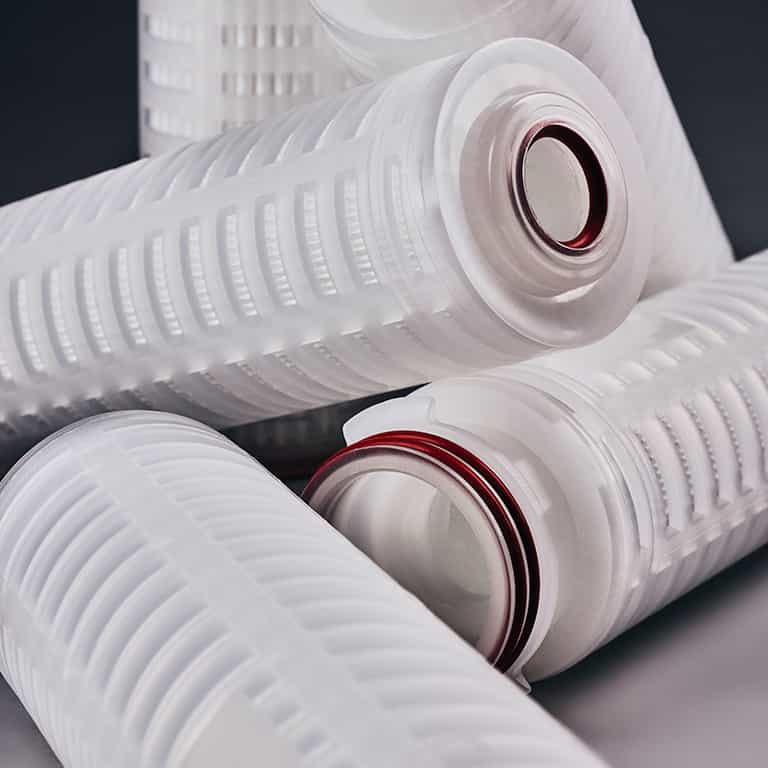
TB-025 Digital Printing Inks
For digital printing inks, filtration is crucial to ensure print quality and minimize downtime. Different ink types (pigment-based, dye-based, solvent-based, and UV curable) require specific filtration methods to remove contaminants, agglomerates, and oversized pigments, optimizing image quality.
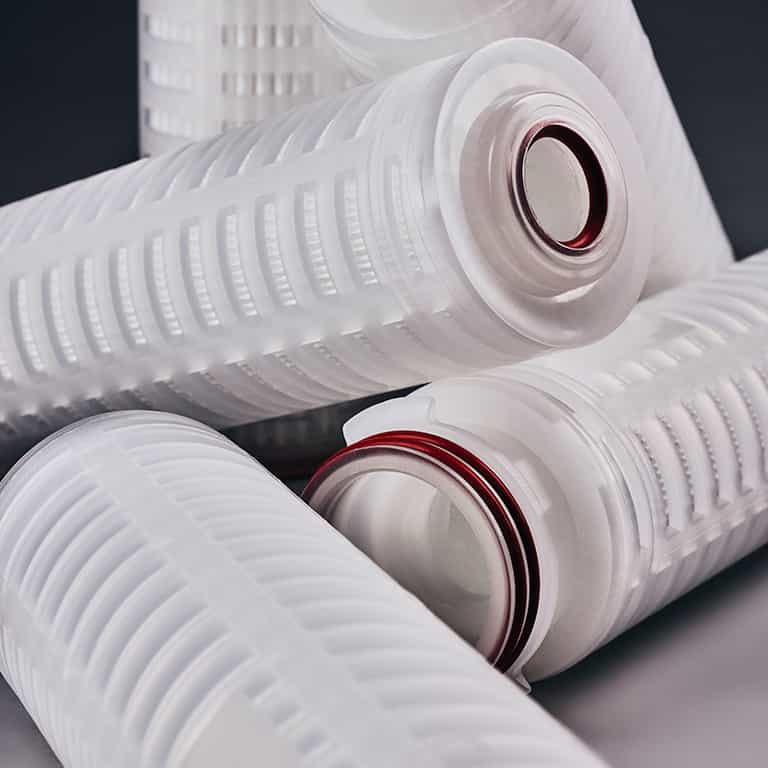
Cleaning/Sanitizing Filters
This technical brief provides the Cleaning and Sanitizing Procedure for Graver Filter Products.
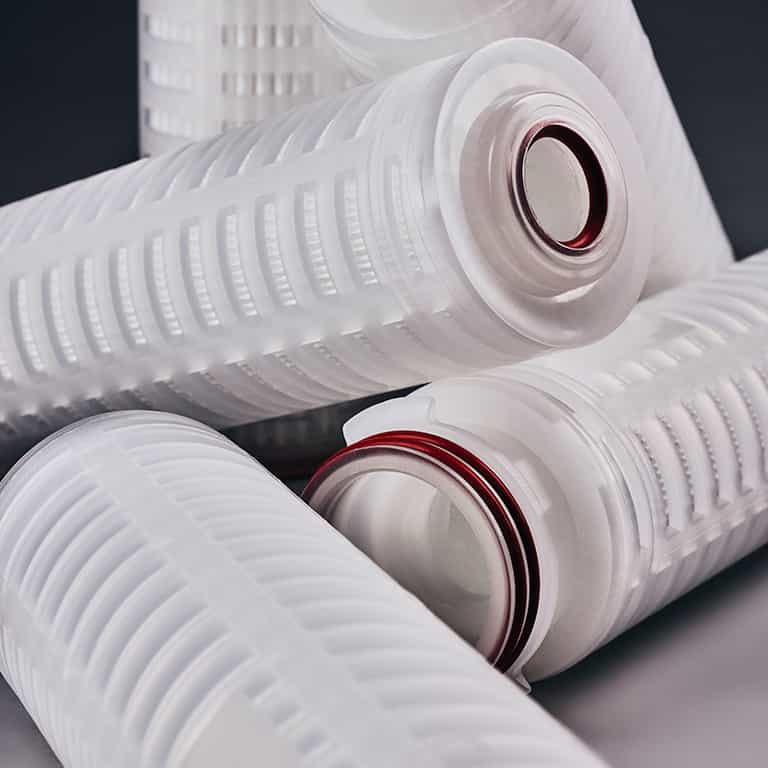
TB-002 QXL Applications
Enhance semiconductor wafer manufacturing with QXL Series slurry filtration, reducing defects and improving yields in CMP processes.
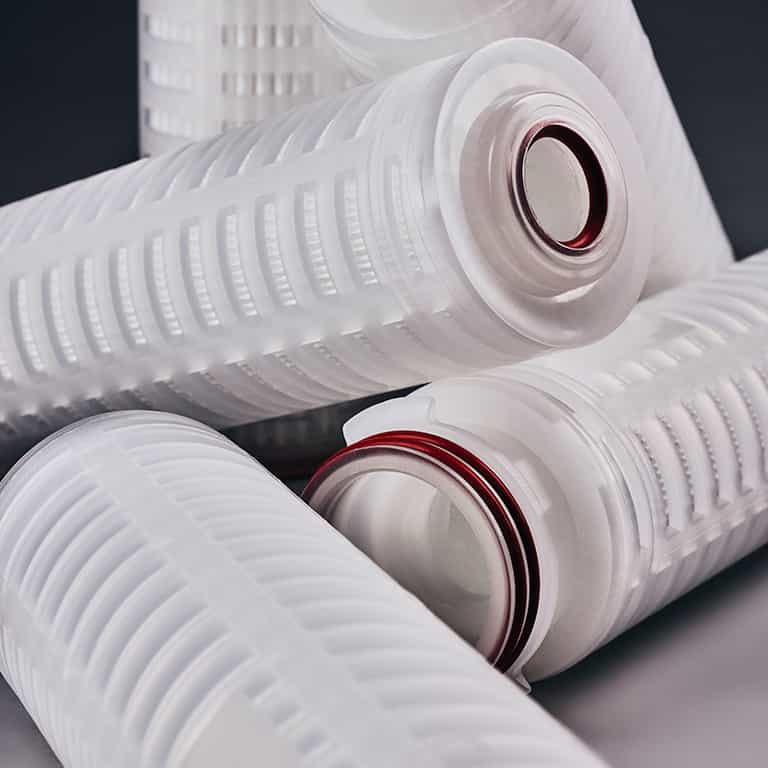
TB-015 Silt Density Index
This technical brief discusses the importance of Silt Density Index (SDI) testing in reverse osmosis (RO) systems to predict and prevent membrane fouling, particularly when producing drinking water from seawater. Maintaining a low SDI value is crucial to minimize fouling and maintain membrane performance.
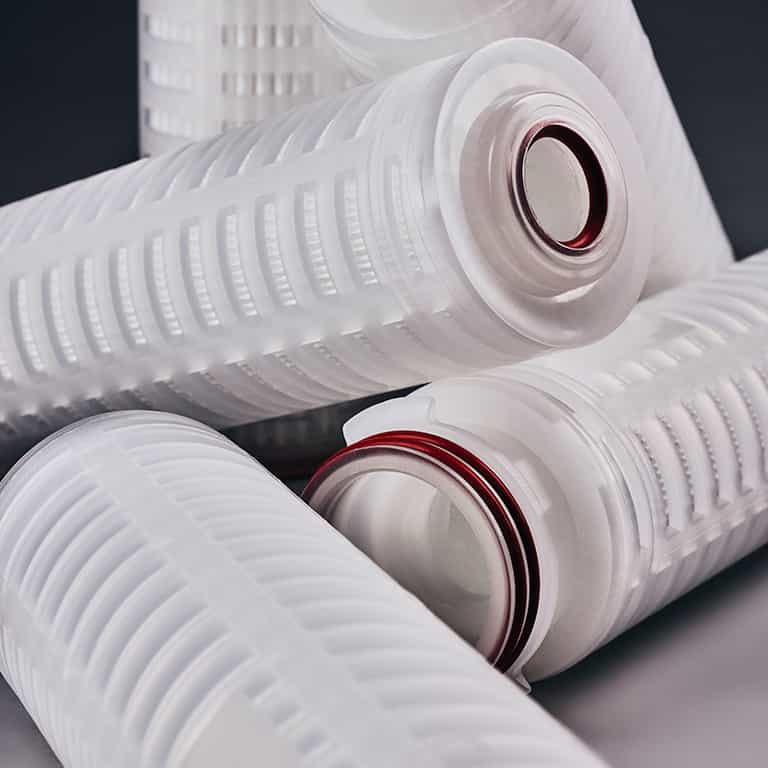
Cleaning/Regeneration
This document explores the Suggested Cleaning/Regeneration Method for Porous Metal Filters.
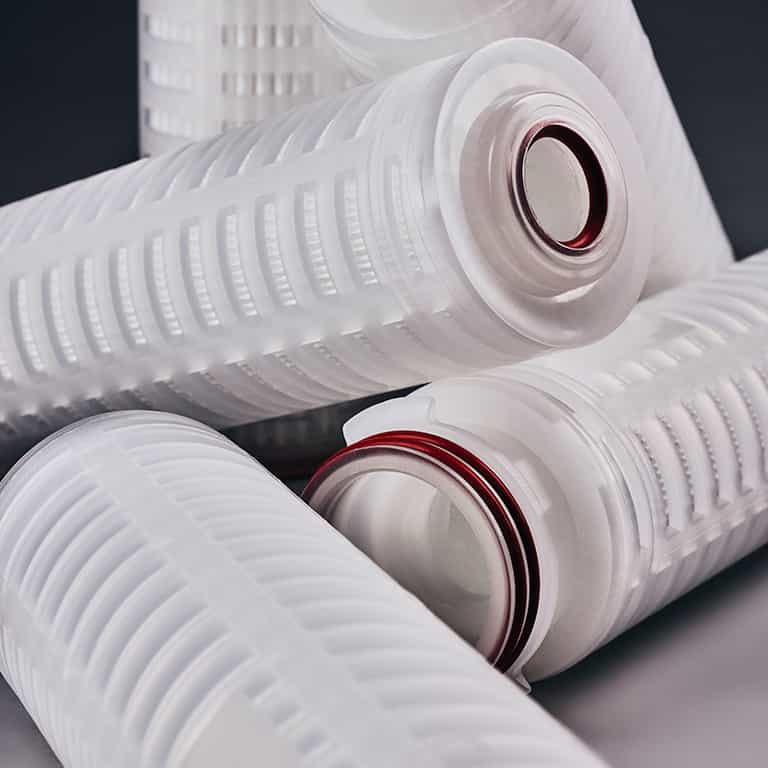
TB-011 Cyst Reduction in Water
This technical brief discusses the challenges posed by Cryptosporidium parvum and Giardia lamblia, protozoan contaminants in water. It explores their resistance to common disinfection methods and the need for effective removal, especially in municipal water systems.
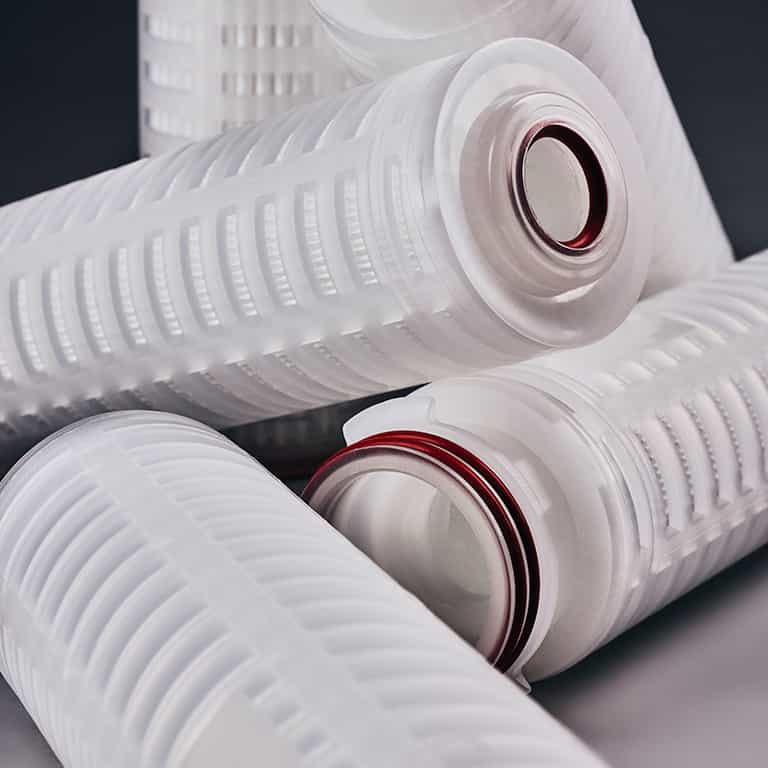
TB-012 High Flow Sizing
This technical brief contains Housing Sizing Guidelines for Graver High Flow Filter Cartridges.
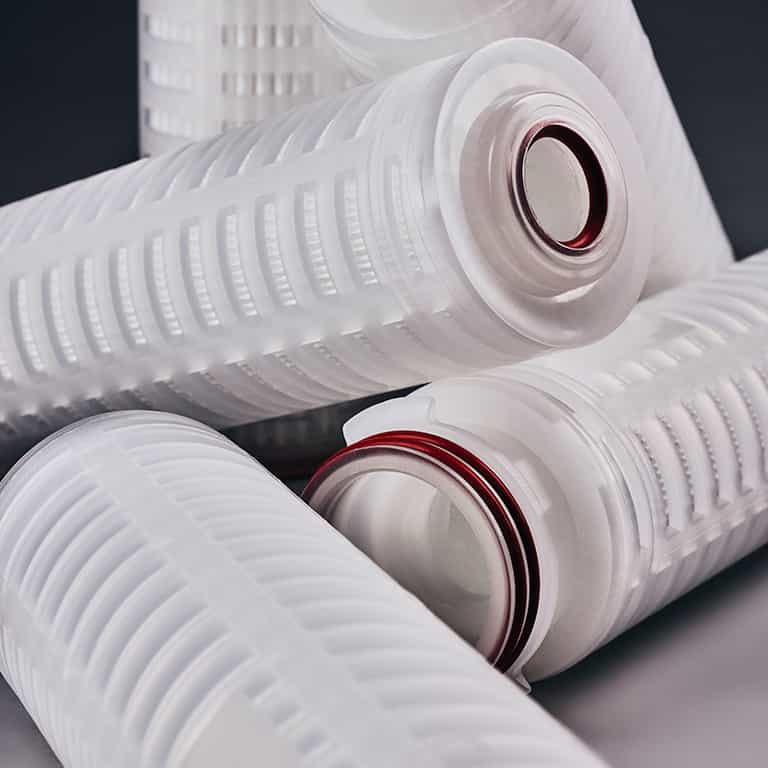
TB-016 End Configurations
Use this technical brief to explore Graver Technologies' wde variety of end configurations for liquid filter cartridges.
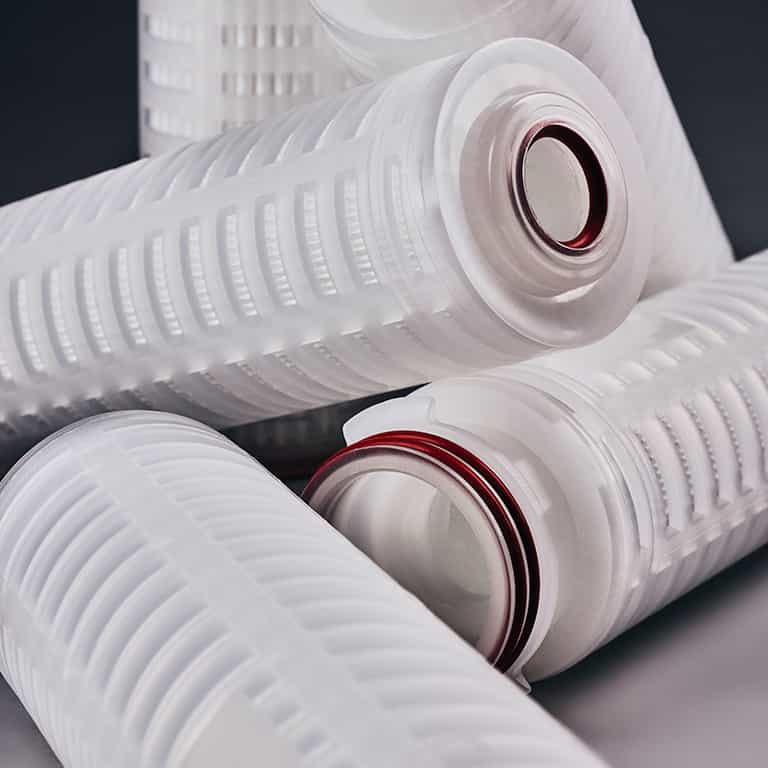
TB-022 Deep Well Injection
This document discusses the importance of filtration in liquid processing, focusing on deep well injection sites. It emphasizes the need for effective filtration to maintain the quality of injected fluids and avoid clogging.
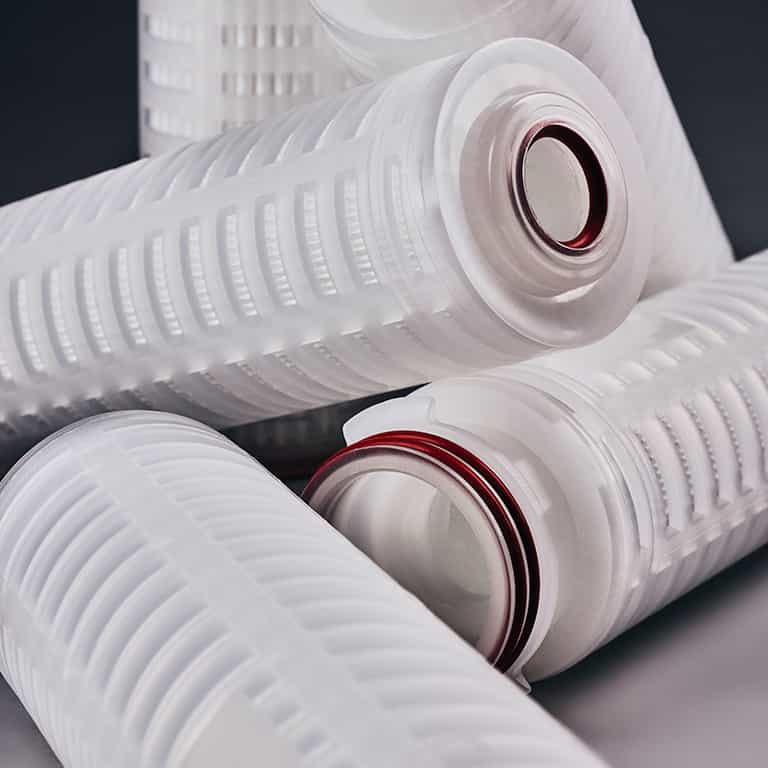
TB-023 Filter Change-out : Law of Diminishing Returns
This document contains information on the concept of diminishing returns in filtration, specifically how adding more filters can impact flow resistance and pressure differentials, as well as recommendations for when to change filters for optimal performance.
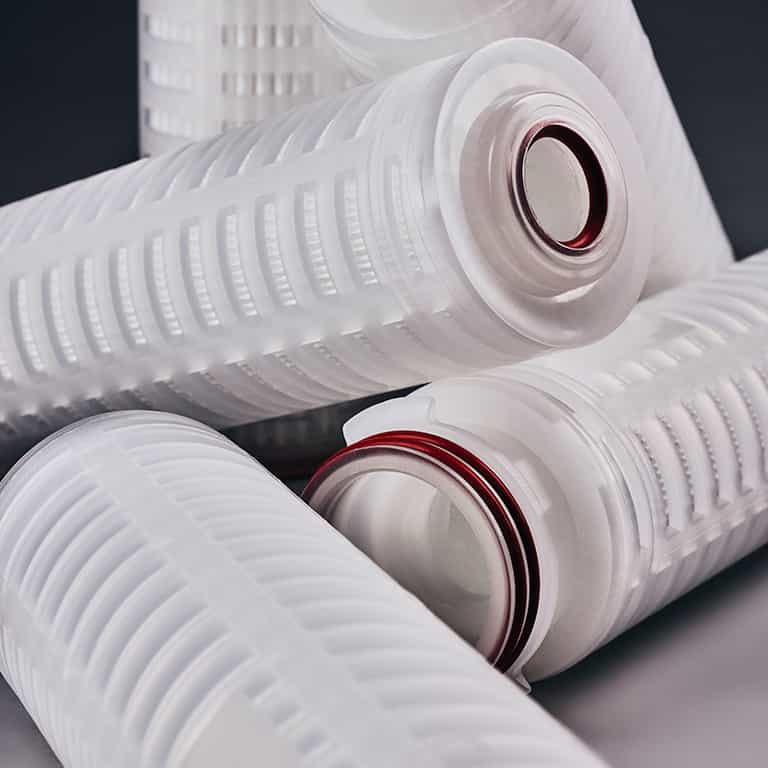
TB-014 Glossary of Biotech Terms
Every industry has an abundance of terms that may be used to describe products and processes. Because of the critical nature of the pharmaceutical and biotechnology markets and the fact that it is highly regulated, it is critical to define and understand some of the more common terms.
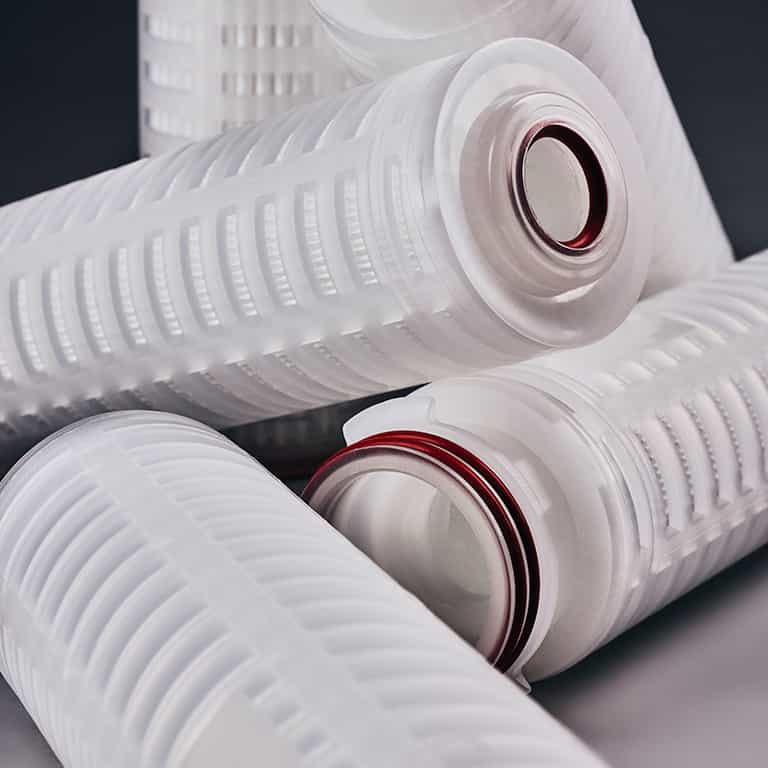
TB-013 Membrane Role in Microbial Retention
This technical brief explores the role of membranes in microbial retention.
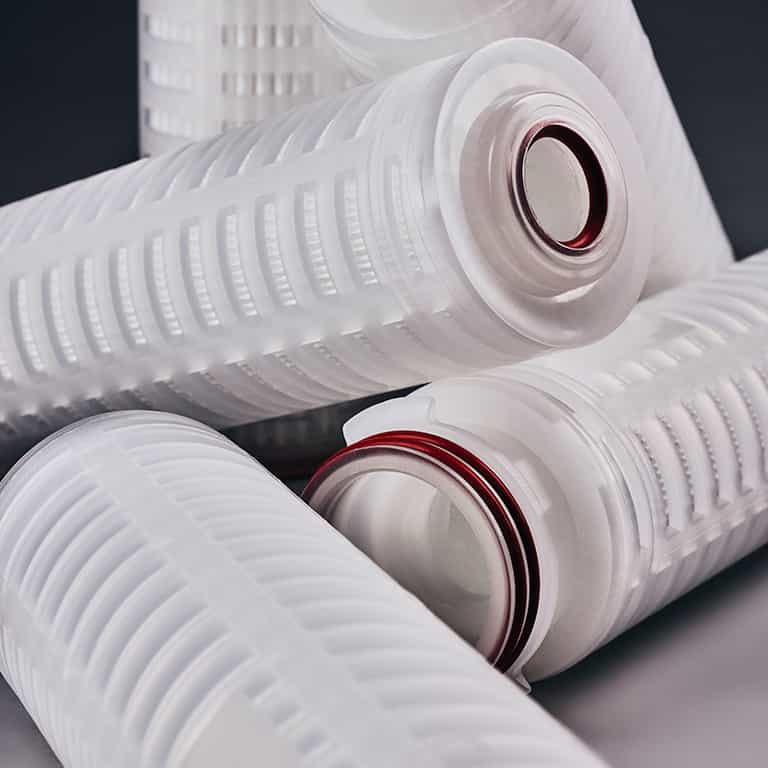
TB-004 Backwashing of Microfiltration Cartridge Elements
This technical brief discusses the backwashing of microfiltration cartridge elements, a process used to clean filters by reversing flow to remove particles and extend filter life, particularly in applications like catalyst recovery and beer and wine filtration.
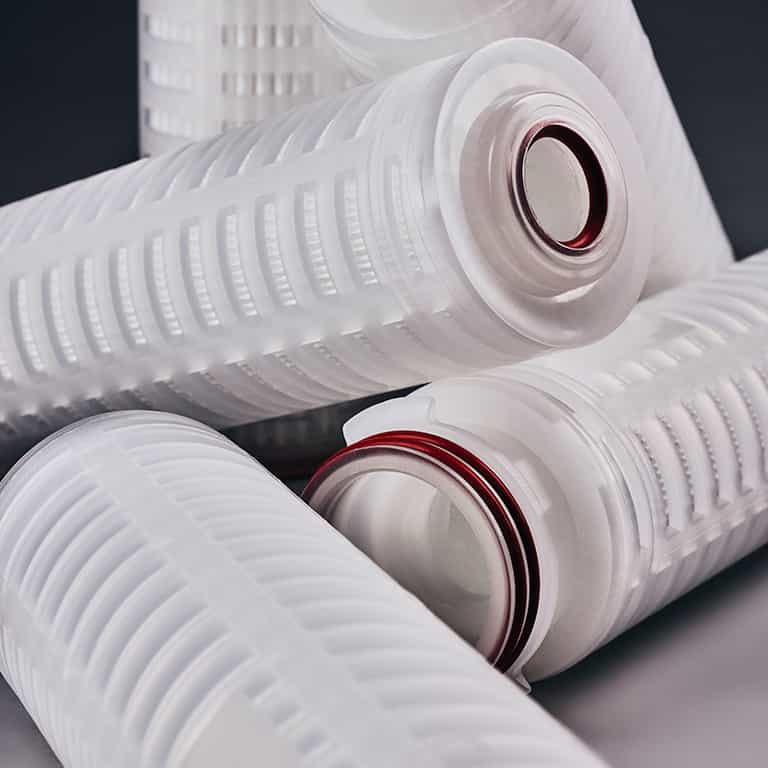
TB-008 Graver Cartridge Regeneration Procedures for Wine & Beer Applications
Explore Graver Technologies' Cartridge Regeneration Procedures for Wine & Beer Applications.
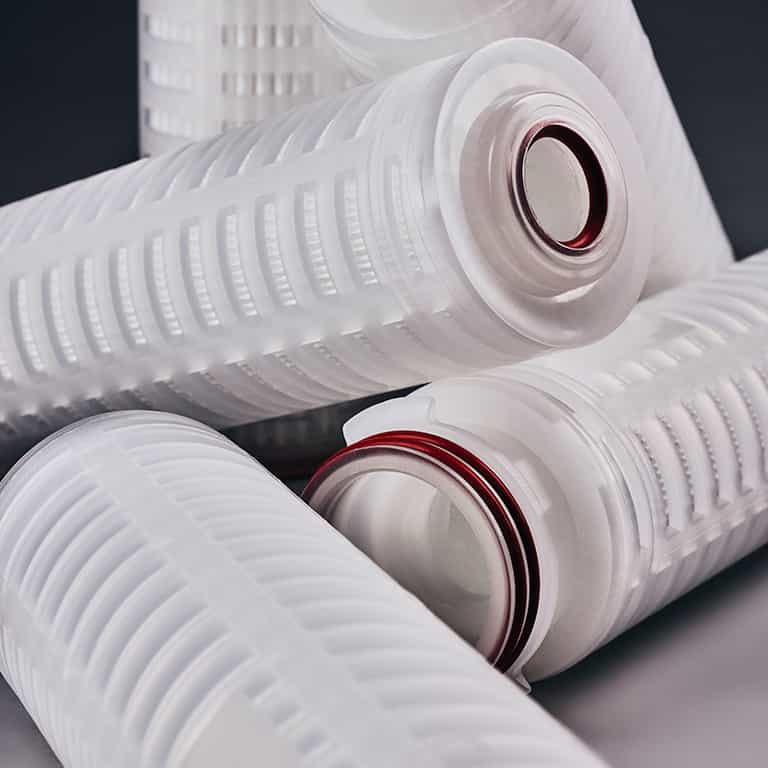
TB-017 Membrane Wetting
This technical brief explores Pre-Wetting Hydrophilic Membranes for Integrity Testing.
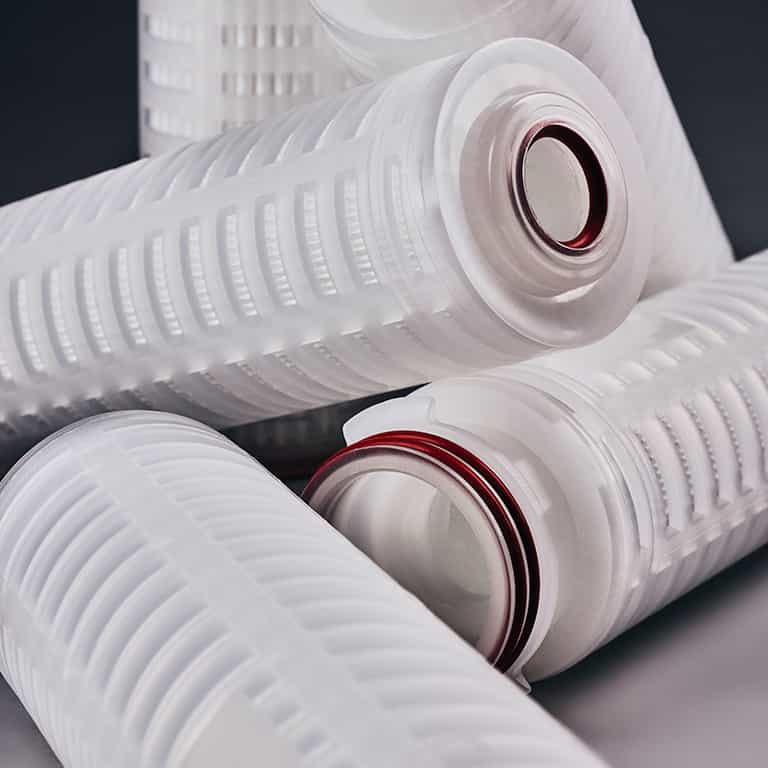
TB-018 Integrity Testing: Pressure Hold
This technical brief identifies why integrity testing is crucial for membrane filters in bioburden control. Bubble point and diffusive flow are common, but Pressure Hold Test is recommended for multi-round housings.
.jpeg)
High Flow Series
The High Flow Series filters handle high flows with fewer elements and offer excellent dirt holding capacity. Smaller systems are possible, reducing upfront costs.
- 6" diameter, large geometry for high flow rates
- Absolute retention ratings from 1 to 100 microns
- Capable of flow rates up to 500 GPM in a single 60" element
- Insideout flow retains contaminant even during changeout
- Multi layer pleated construction with optimized surface area
- Outer cage prevents media extrusion problem experienced with some competitive offerings
- Unique Quad Seal gasket provides maximum seal integrity
- Retrofits competitive high flow filter housings
- Thermally bonded construction
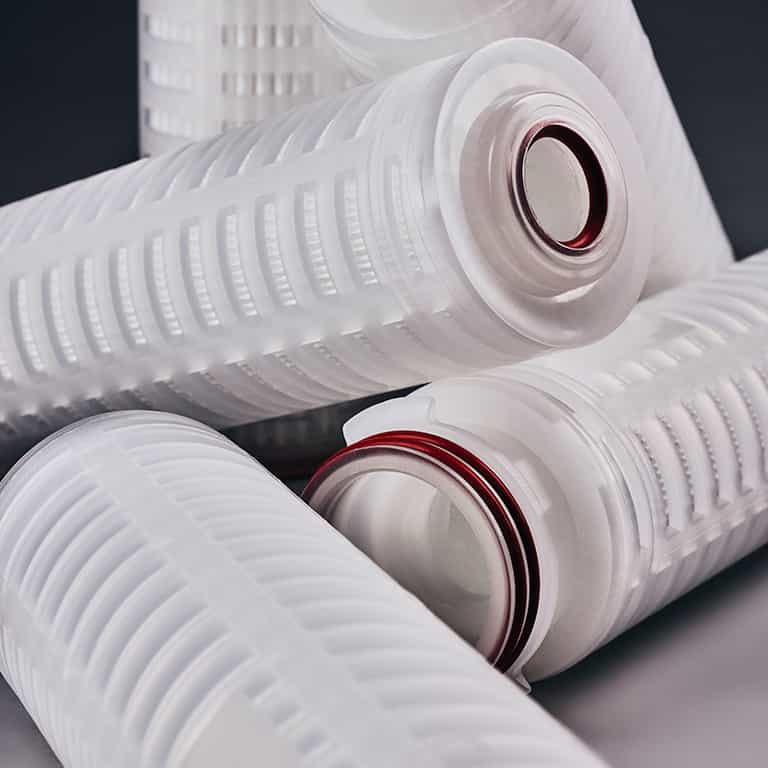
ACS-014 Post Carbon Treatment
This case study discusses how Graver Technologies was able tp help a Sterile Injectables company achieve better post-carbon bed treatment for improved final product.
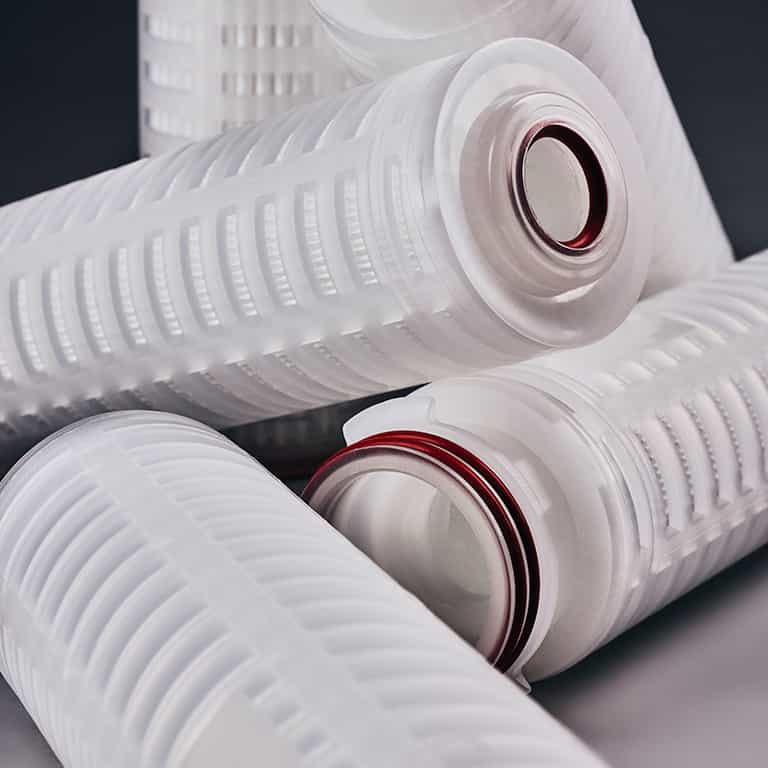
ACS-005 Stratum Filters Clarify Optical Coatings
This application case study looks into improving optical coatings for specialty faceplates used in military applications to ensure clarity and reduce defects.
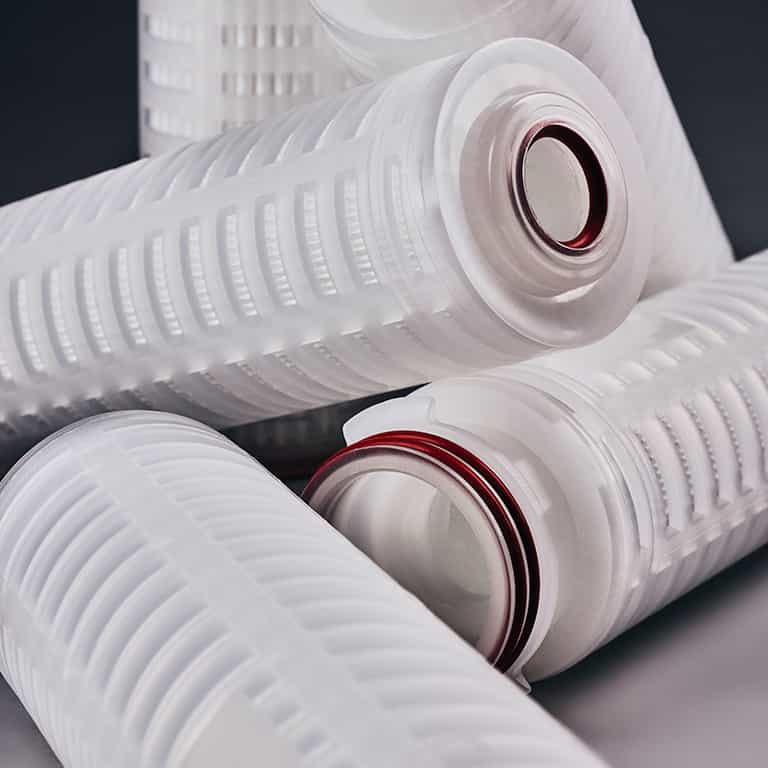
ACS-008 Citric Acid Plant Condensate Water
This case study details how Graver GFP 1-30P7E filters improved condensate water filtration for a citric acid plant, overcoming rust and dirt issues.
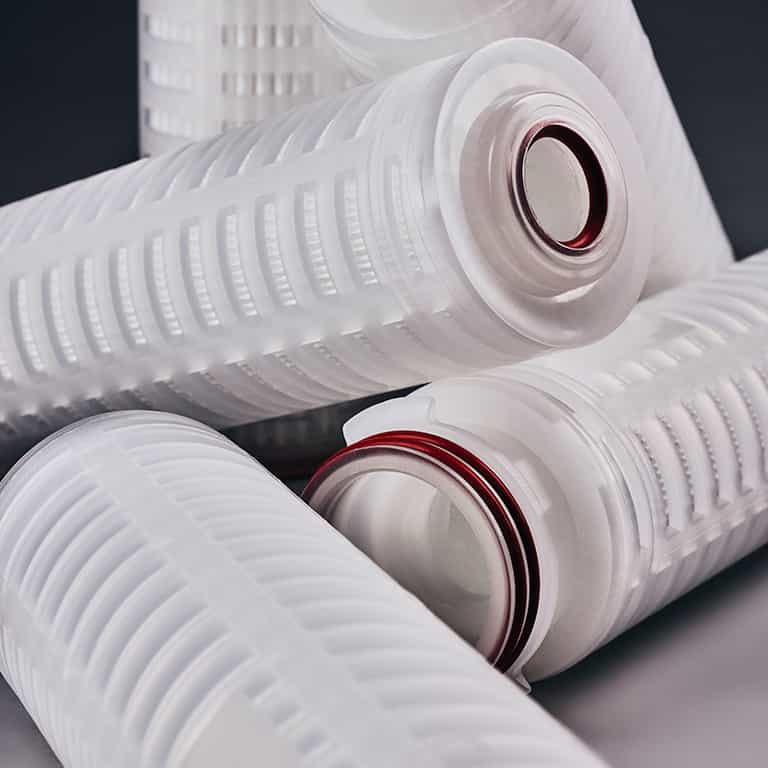
ACS-004 - Tank Vent for Citrus Juice
This application study focuses on the use of PTFE membrane filters in a citrus juice processing plant to prevent juice spoilage.
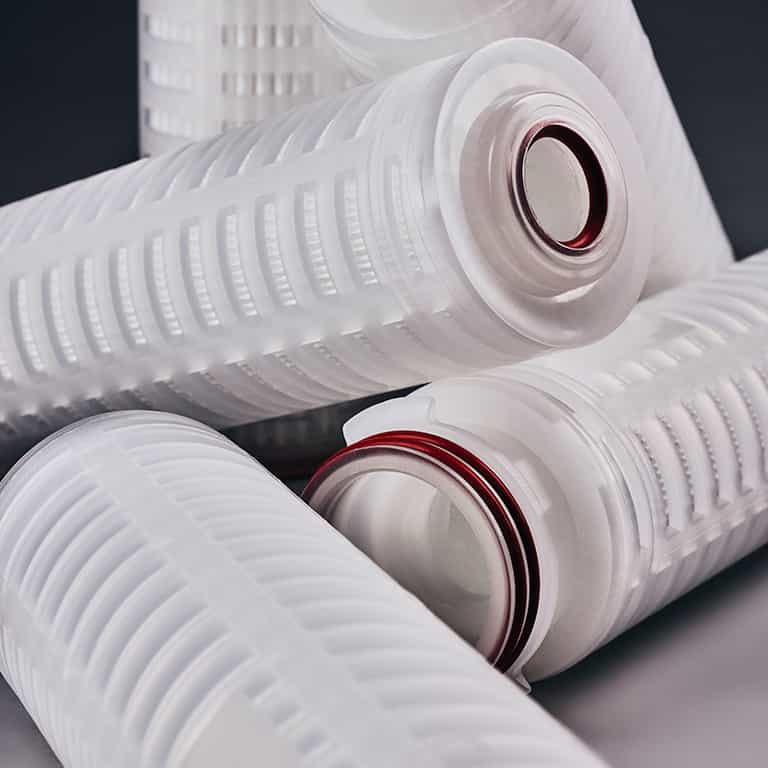
ACS-012 Pleated Filters for Pre RO
This case study highlights how Graver PMC pleated filters improved filtration efficiency in a high purity water system as pre-RO filters, leading to reduced maintenance and labor costs.
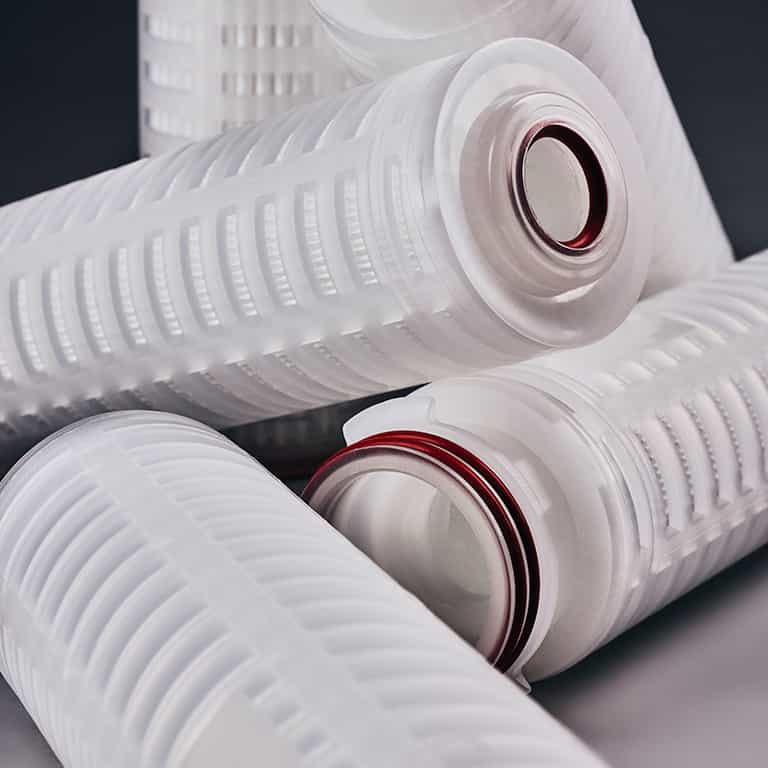
ACS-011 Wafer Grinding for Integrated Circuits
This case study discusses the use of filtration in the semiconductor wafer manufacturing industry, specifically in the process of wafer backgrinding for integrated circuits.
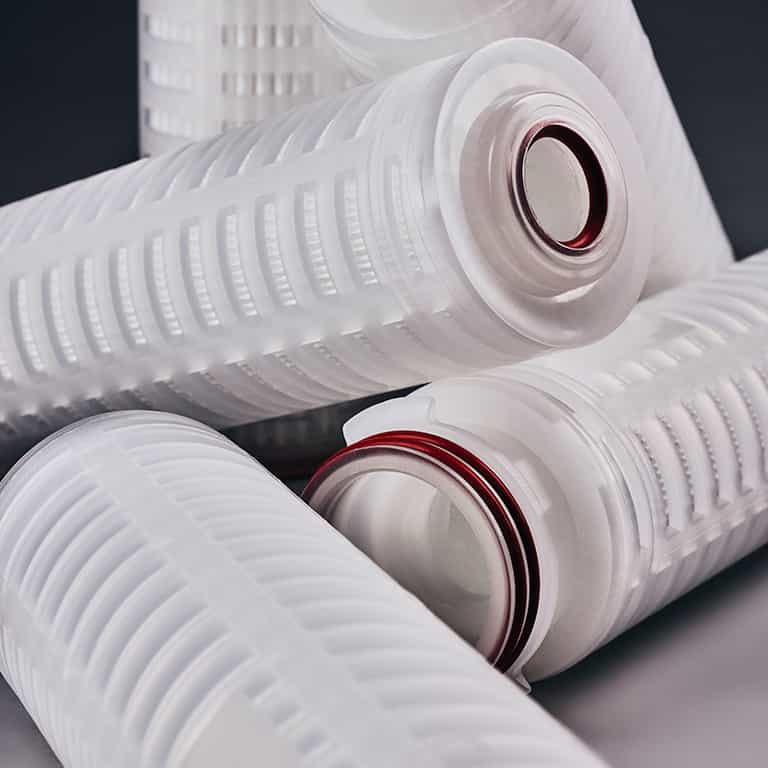
ACS-006 Chilled Water Loop High Flow
This case study highlights how High Flow Filters effectively cleaned a Chilled Water Loop, reducing contamination and maintenance costs.
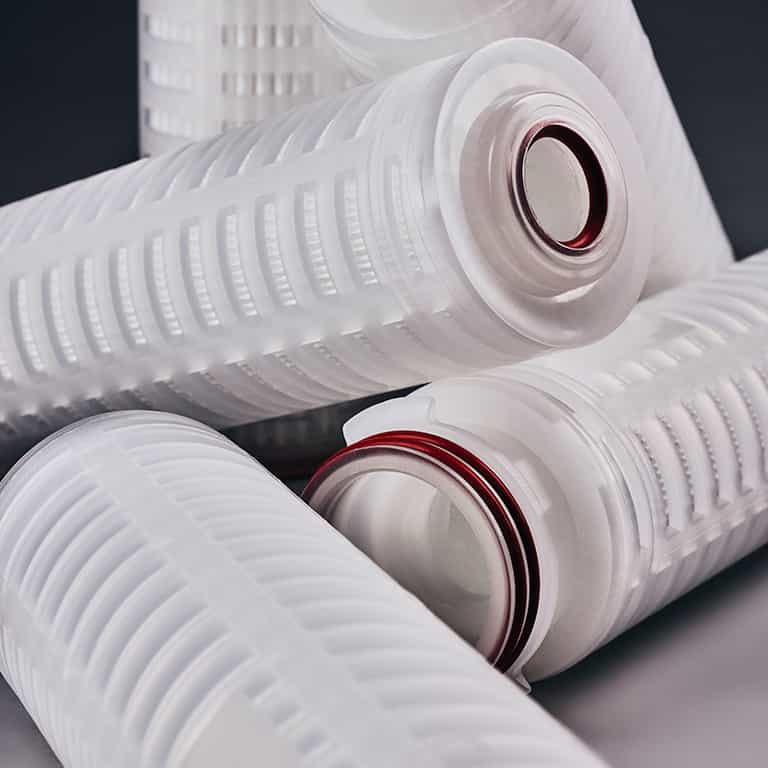
ACS-001 - Offshore Water Treatment
This application case study explores a customer's search for cost-effective filtration alternatives to high-priced Pall High Flow Ultipleat filters, driven by concerns over operational costs, filtration efficiency, and operator safety.
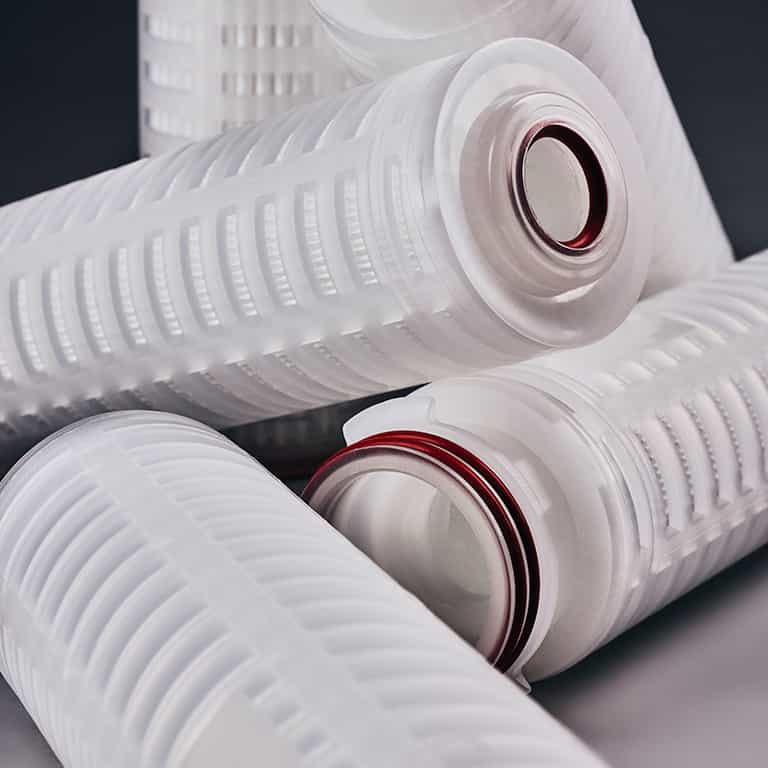
ACS-010 Water Quality for Animal Herds
This case study explores the importance of water quality in the context of animal herds, specifically focusing on improving filtration efficiency for RO membrane protection in dairy farms.
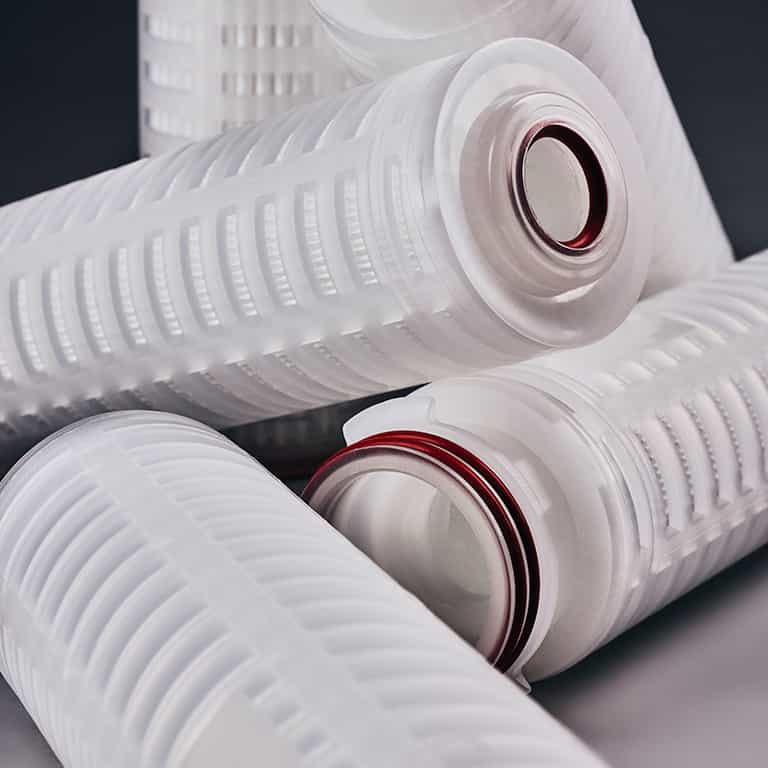
ACS-007 Sausage Casings Stratum
This case study explores how Graver Stratum C 3 micron filters improved filtration efficiency and saved costs for a sausage casing manufacturer.
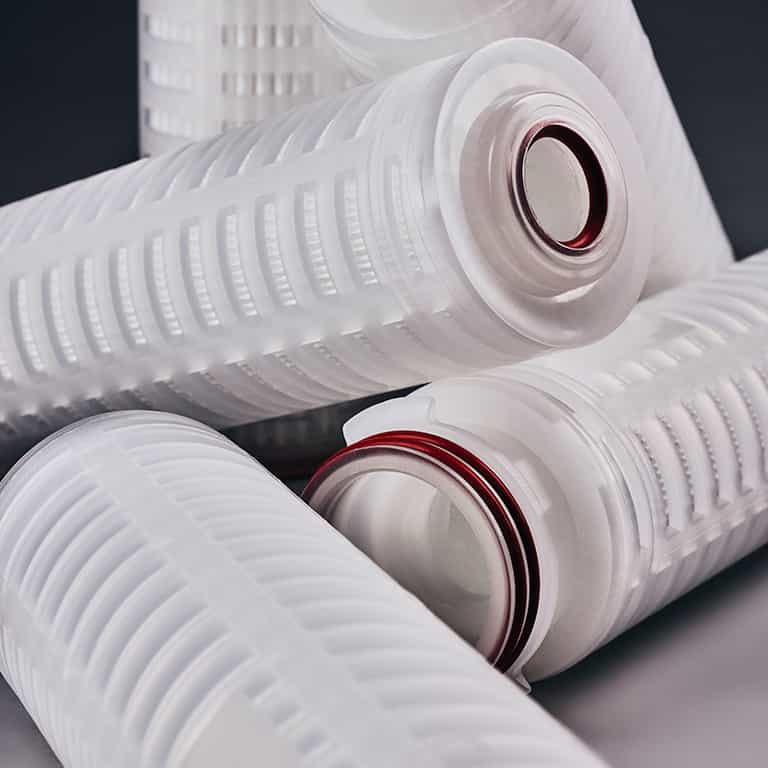
ACS-003 - Pre-RO for Ethanol Plant Apple Case Study
This application case study focuses on the use of Graver MBF series filters in an ethanol production plant to protect RO membranes and meet water quality requirements for various processes.
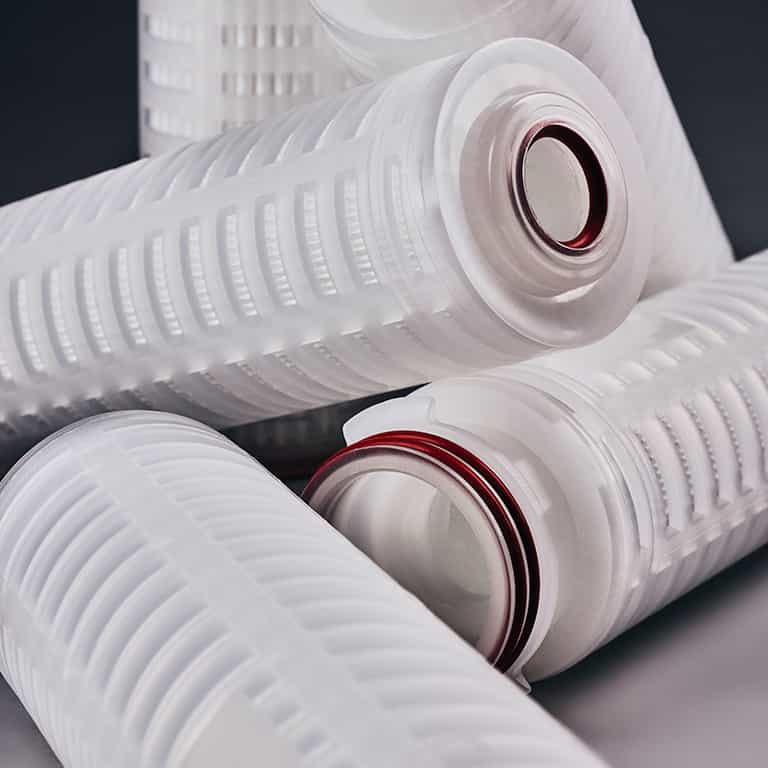
ACS-009 - Bottled Water Applications Case Study
This case study discusses the filtration processes and challenges in the bottled water industry, focusing on improving water quality and cost savings using Graver High Flow cartridges.
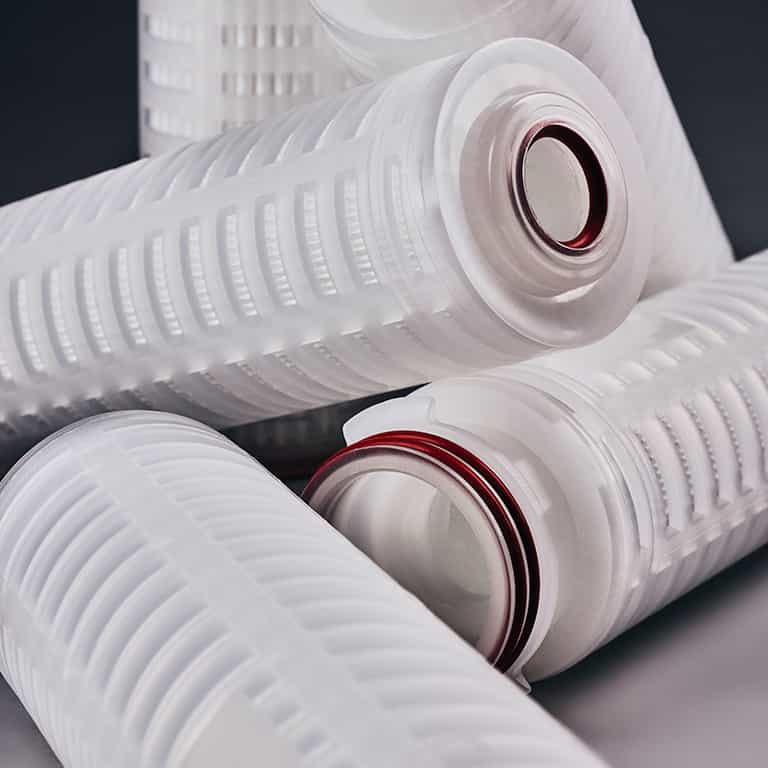
ACS-013 CBD Oil
This case study discusses the filtration of CBD oil from Cannabis and Hemp plants, focusing on the recovery and purification process for this natural product.
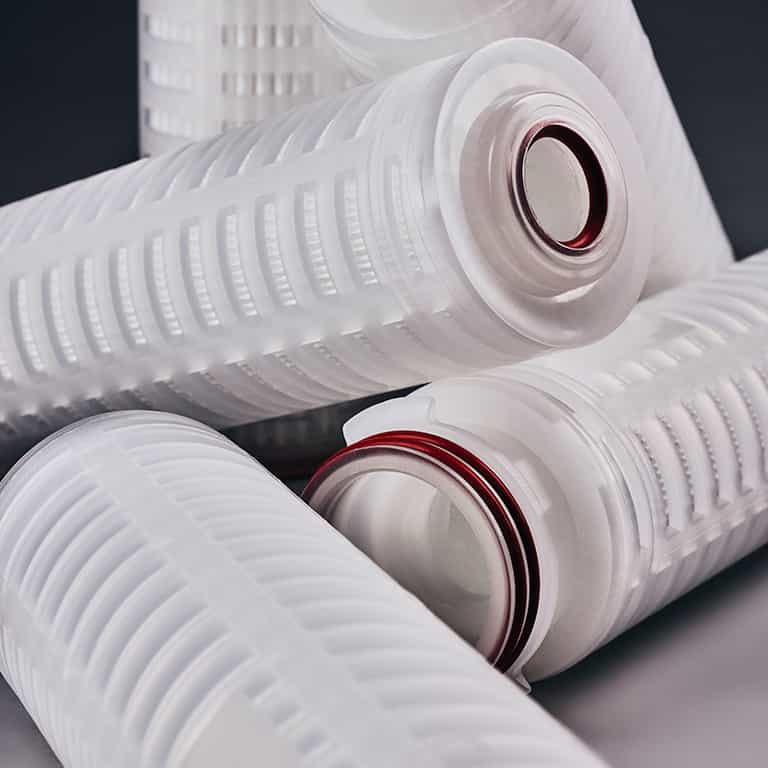
ACS-002 - Ink Jet Ink Appl Case Study
This application case study focuses on a solvent-based ink manufacturer's quest to effectively remove agglomerated particles while preserving colored pigments.
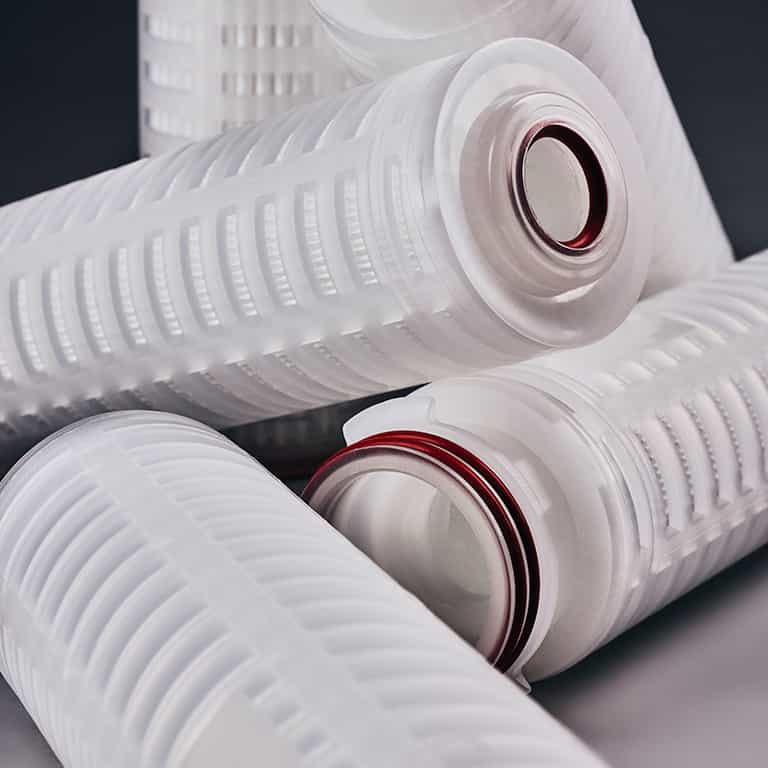
AB-008 High Flow Filters for Pre RO
This application brief explores the effectiveness of Reverse Osmosis (RO) in removing contaminants from water. It emphasizes the importance of membrane pretreatment using high-performance pleated filter cartridges to extend membrane life, reduce operational expenses, and minimize environmental impact.
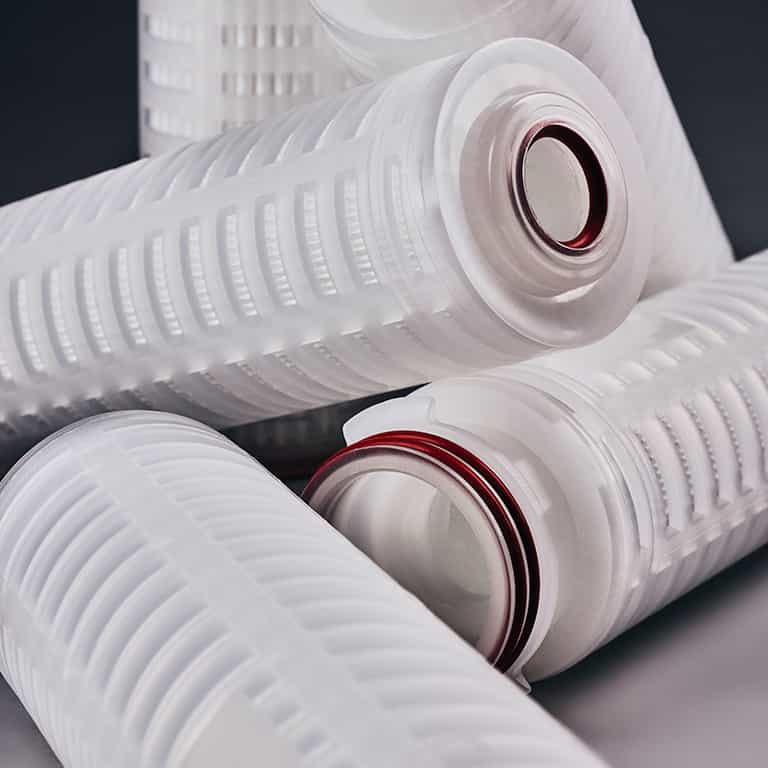
AB-006 Focused Microelectronics Applications
This application brief explores filtration opportunities in various microelectronics applications, including Light Emitting Diodes (LEDs), Photovoltaic Cells (Solar Cells), and Flat Panel Displays (FPDs).
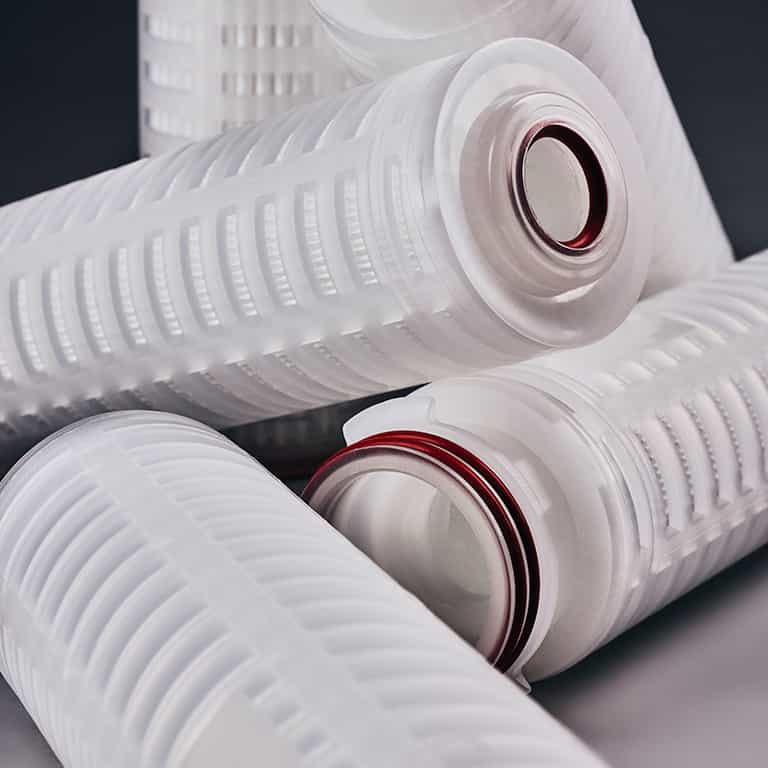
AB-005 Basics of Manufacturing Integrated Circuits
This application brief explores the filtration requirements in the manufacture of integrated circuits, including various electronic components like transistors, capacitors, resistors, diodes, LEDs, and photocells.
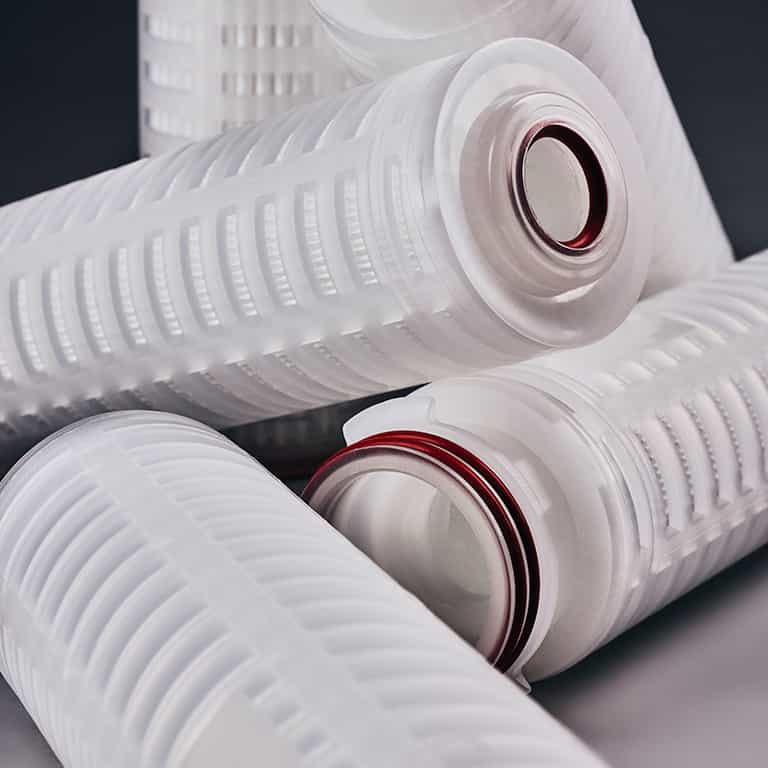
AB-002 Vent Filtration
This case study explores the essential aspects of vent filtration, focusing on system sizing considerations for tank vent filters. It also emphasizes the importance of proper air flow to protect tank contents from contaminants.
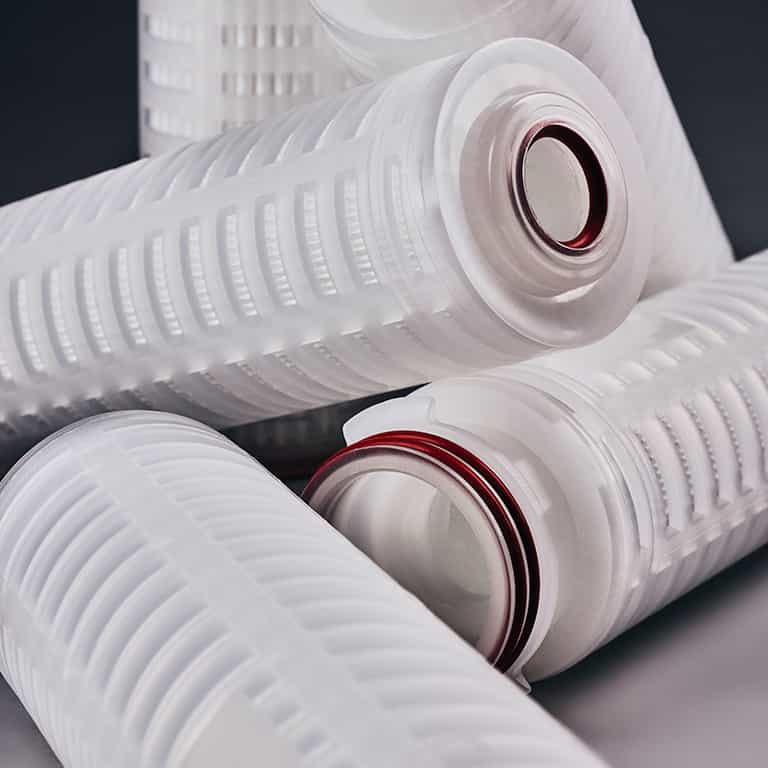
AB-003 - Filtration Opportunities in Pulp and Paper
This case study explores numerous filter applications for Graver liquid process filters and can benefit from the superior performance of Graver’s Stratum, MBC and RTEC Series filters.
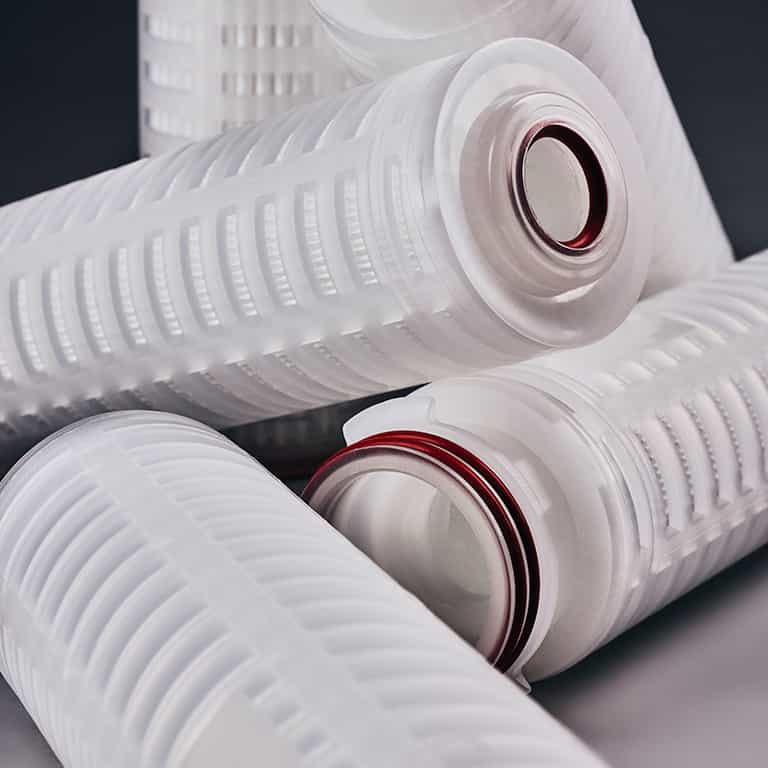
AB-001 - Seal Flush
This case study explores the comparison between resin-bonded and melt-blown filter cartridges for industrial applications, specifically in protecting seals of rotating equipment in environments like Pulp and Paper mills.
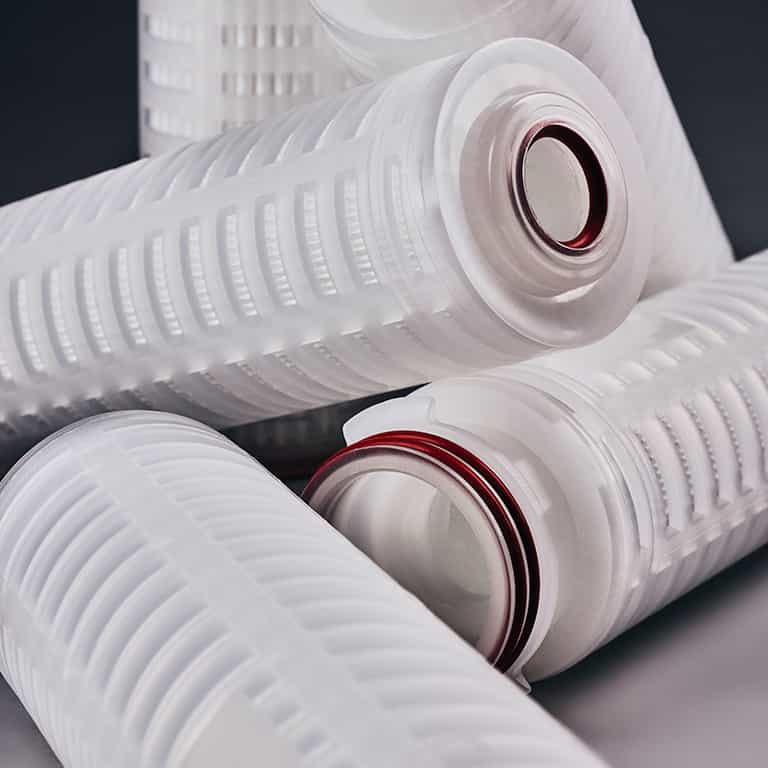
AB-004 - Filtration Opportunities with Microbreweries
This application explores filtration opportunities within the microbrewery industry. It discusses various filtration steps in the brewing process, such as clarification following fermentation and microbial stabilization prior to bottling.
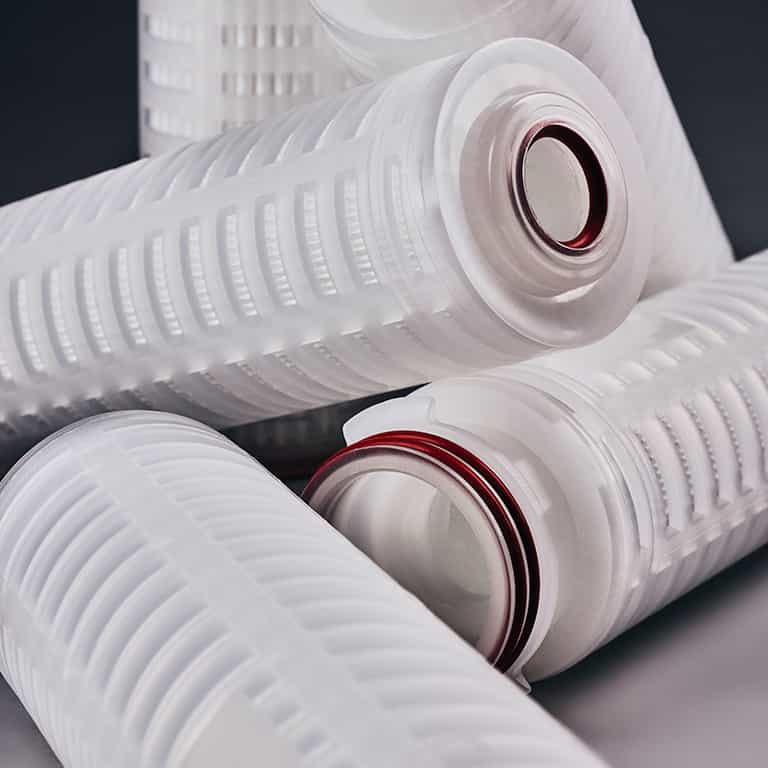
TB-022 Deep Well Injection
This document discusses the importance of filtration in liquid processing, focusing on deep well injection sites. It emphasizes the need for effective filtration to maintain the quality of injected fluids and avoid clogging.
Products
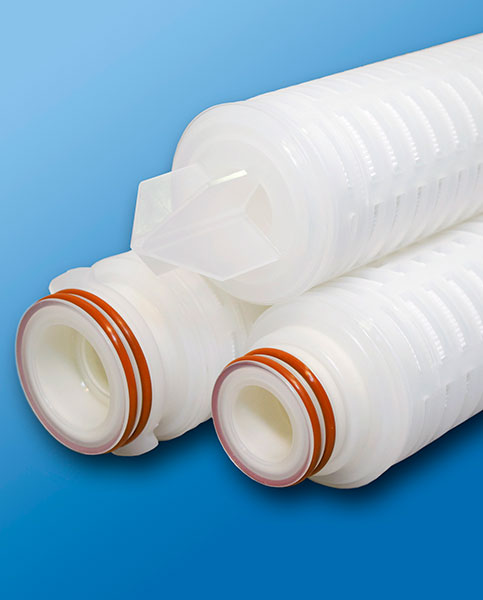
ZTEC™ P Series
ZTEC™ P Sterilizing Grade membrane cartridges are validated for complete bacterial retention to yield product sterility in biopharmaceutical final filtration applications.
- Manufactured in an ISO Class 7 Cleanroom Environment
- 100% flushed with ultrapure DI water
- Meets ASTM Standards for Sterility
- Repeatably Steamable/Sanitizable
- 100% Integrity tested prior to release
- Pore size, lot and serial number are stamped on each filter element for identification and traceability
- Complete validation guide available
.jpeg)
QSL™ Filter Series
The QSL™ cartridge has a polypropylene microfiber media over a polyethersulfone membrane. It's design offers excellent retention characteristics and extended life.
- Serial layered design — enhances capacity and simplifies prefiltration requirements
- Absolute rated (99.98%) — an ideal prefilter to 0.2, 0.45 and 0.65 micron membrane filters
- Fixed pore construction — resists dirt unloading at maximum differential pressure
- High surface area — high flow rate, and long service life — minimize maintenance cost
- Available with various gasket/Oring materials — compatible with many fluids
.jpeg)
QCR™ Series
An absolute rated filter designed to meet or exceed the minimum log reduction credit of >3.0 for cysts.
- Constructed of polypropylene or polypropylene and polyethersulfone — compatible with most fluids
- Double ORing style ends for the highest seal integrity
- 7.0 ft2 (0.65 m2) of effective filter area
- Various ORing materials and configurations — easily retrofits most systems
- High surface area — high flow rates and long online service
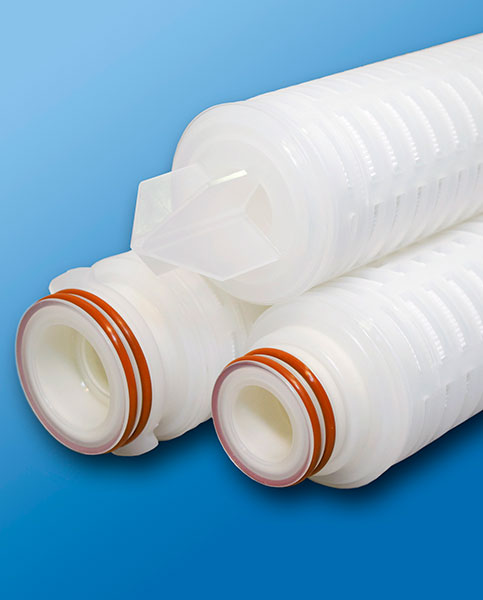
ZTEC™ WB Series
ZTEC™ WB cartridge filters use PES membrane to remove spoilage organisms and inorganic particulate to protect beverages.
- Manufactured in an ISO Class 7 Cleanroom Environment
- 100% flushed with ultrapure DI water and integrity tested
- Low adsorption of protein, color and flavor components
- Steamable/sanitizable for cleaning and reuse
- High log reduction values for spoilage organisms
- PES membrane provides high capacity contaminant loading
- Complete qualification guide available
- Quick wet treatment available
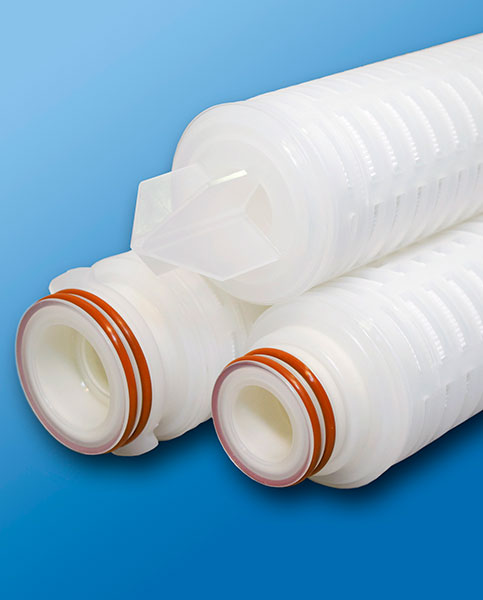
ZTEC™ G Series
This pleated, disposable filter element is constructed of absolute rated, hydrophilic, asymmetric polyethersulfone membrane with extended filter area.
- 7.0 ft2 (0.65 m2) of membrane surface area per 10" element — High throughput, longer online service reduces costly maintenance time
- Absolute rated membrane from 0.1 to 0.65 μm
- Manufactured in an ISO Class 7 cleanroom environment
- 100% flushed with 18 MΩ cm DI water and gross integrity tested
- Fixed pore construction eliminates dirt unloading as differential pressure increases
- Low extractables
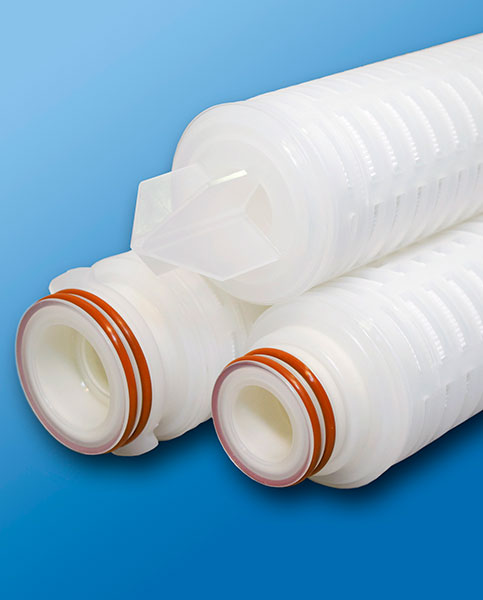
ZTEC™ E Series
The ZTEC™ E microelectronics grade cartridges by Graver are designed for ultrapure water filtration, and are hydrophilic and free of added surfactants to avoid contamination of water streams.
- Manufactured, flushed, tested and packaged, in an ISO Class 7 Cleanroom Environment
- Filters are 100% flushed with 18 MΩcm DI water and integrity tested
- Resistivity rinse up to 18 MΩcm and single digit ppb TOC levels with minimal throughput
- Available in a variety of end cap/adapter configurations to fit all industry standard housings
- Pore size, lot and serial number are stamped on each filter element for identification and traceability
- Complete qualification guide available
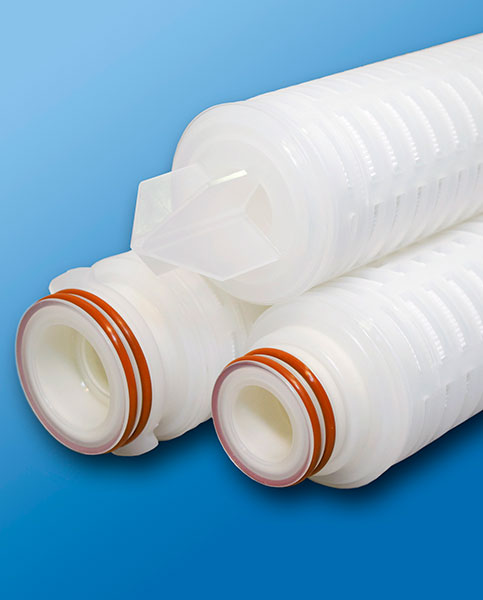
ZTEC™ B Series
ZTEC™ B Bioburden Reduction grade membrane cartridges provide highly consistent performance for bioburden reduction and particle removal across a wide range of beverage, pharmaceutical and biological fluids.
- Manufactured in an ISO Class 7 Cleanroom Environment
- 100% flushed with ultrapure DI water and integrity tested
- Repeatably steamable/sanitizable
- High retentions up to 107/cm2 challenged for bacteria and yeast
- Pore size, lot and serial number are stamped on each filter element for identification and traceability
- Complete qualification guide available
.jpeg)
WaterTEC™ Series
The WaterTEC™ filter series is constructed of absolute rated, hydrophilic, asymmetric polyethersulfone membrane and polypropylene components.
- Low pressure drop reduces energy costs
- High dirt holding capacity minimizes changeouts and down time
- All thermal bonded construction with no adhesives
- Available in all common configurations to allow use of existing filter housings
- Cost effective absolute filtration
Contact Us
If you have questions or comments regarding the information in this site, or if you wish to receive additional information on Graver Technologies, please contact us: